
Receivers vs. Loaders – What’s the Difference?
Before we dive into choosing the right vacuum receiver, let’s clear up a common industry mix-up. Many processors use the terms “loader” and “receiver” interchangeably, but they’re not the same thing.
Here’s the key difference:
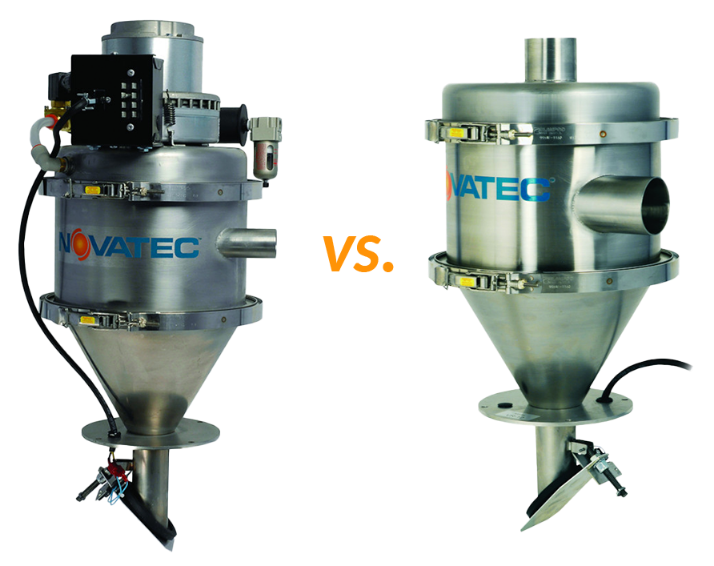
- Self-Contained Loaders have a built-in motor. They’re independent units that pull material directly from a nearby storage bin or gaylord to a processing machine—over short distances.
- Vacuum Receivers don’t have a motor of their own. Instead, they rely on a central vacuum pump to pull material from a shared source to multiple machines, handling anything from short runs to longer distances across your plant.
So, if you’re looking for a guide on self-contained loaders, check out our Ultimate Guide to Loaders. But if you’re working with a central material handling system or considering an upgrade—keep reading, because we’re about to break down everything you need to know about vacuum receivers.
1. Why Vacuum Receivers Are Essential for Plastics Processing
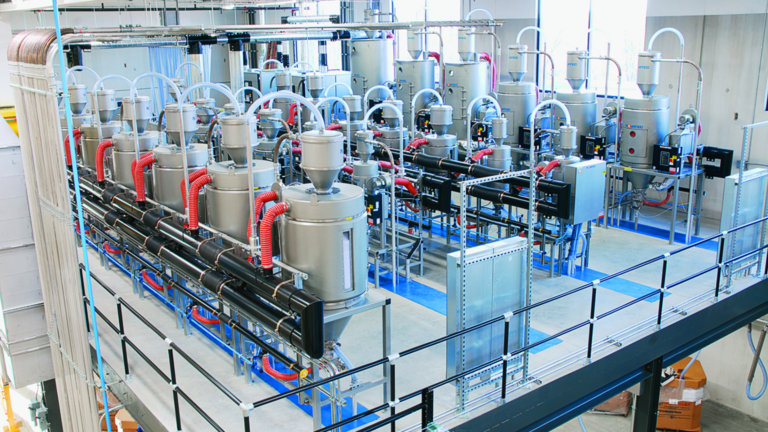
Material handling is the backbone of production—when it’s running smoothly, you don’t even think about it. But when it’s not? It quickly becomes the biggest problem in the plant.
An inefficient or unreliable vacuum receiver doesn’t just slow things down—it can create costly problems across your operation, including:
- Starved machines – Leading to missed production quotas and costly downtime.
- Clogged filters and blockages – Causing delays, manual cleanouts, and unnecessary labor costs.
- Inefficient material flow – Resulting in overfeeding, inconsistent throughput, or wasted material.
- Frequent equipment issues – Forcing operators to constantly babysit or troubleshoot the system instead of focusing on production.
A well-designed vacuum receiver system keeps your material moving consistently, efficiently, and with minimal maintenance. But not all receivers are created equal—choosing the right one can make a huge difference in uptime, ease of maintenance, and overall efficiency.
So, let’s break down how vacuum receivers work, what features matter, and which ones are right for your operation.
2. How Vacuum Receivers Work in a Central Conveying System
A vacuum receiver is just one part of a larger central conveying system, but it plays a crucial role in ensuring material moves efficiently and reliably. Here’s how all the pieces work together to keep resin flowing:
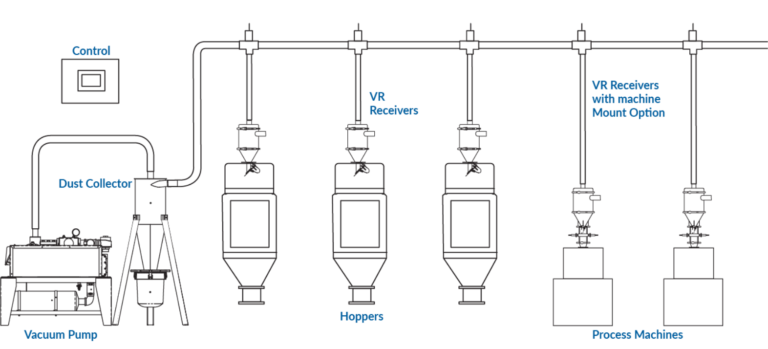
A vacuum receiver is just one part of a larger central conveying system, but it plays a crucial role in ensuring material moves efficiently and reliably. Here’s how all the pieces work together to keep resin flowing:
- Central Control – This is the brain of the operation, coordinating all inputs, outputs, and timing signals to make sure every component works together seamlessly.
- Central Vacuum Pump – Creates the negative pressure that pulls material through the system.
- Dust Collector – Positioned between the receivers and the pump, the dust collector captures fine particles before they reach the pump, protecting it and extending service intervals.
- Sequencing Valve – Tells each receiver when to draw material, ensuring receivers take turns pulling resin to avoid overloading the system.
- Receiver – Mounted above processing machines, blenders, or drying hoppers, the receiver collects the incoming resin and holds it until the destination is ready.
- Discharge Valve – Opens to release the material into the destination below—whether that’s a dryer, extruder, injection molding machine, or blender.
- Level/Demand Sensor – Detects the material level inside the receiver and triggers a demand signal when more resin is needed.
Since vacuum receivers depend on the central vacuum pump, controls, and sequencing valves to function properly, choosing the right pump and control system is just as important as selecting the right receiver. For a deeper dive into vacuum pump selection, check out The Ultimate Guide to Vacuum Pumps for Plastics Processing. And if you want to better understand how central controls tie everything together, you’ll find that covered in The Ultimate Guide to Central Controls for Plastics Processing.
Now that we’ve covered how receivers fit into a conveying system, let’s take a closer look at what separates a great vacuum receiver from an average one.
3. Key Features & Components of a Vacuum Receiver
Not all vacuum receivers perform equally—and choosing the wrong one can lead to inefficiency, downtime, and constant maintenance headaches.
To make an informed decision, you need to understand what makes a great vacuum receiver and how different designs impact performance.
Every vacuum receiver consists of several key components, each of which affects efficiency, maintenance, and longevity.
Lid Design – Standard vs. Hinged
At first glance, a vacuum receiver lid might seem like a small detail—but if you’ve ever had to change a filter while standing on a ladder, you know how frustrating they can be.
Most traditional vacuum receivers use a fully removable lid, meaning:
- It’s heavy and awkward to lift—especially when mounted high.
- It slows down maintenance—Operators avoid cleaning filters because it’s a hassle.
- It increases downtime—If filters aren’t cleaned regularly, airflow suffers, leading to inefficient material flow.
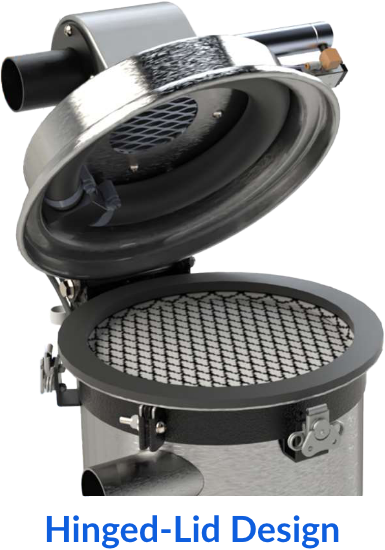
At Novatec, we take a different approach. Our VRX Series features a hinged lid that allows operators to flip it open for quick, tool-free access. No struggling, no downtime—just fast, easy maintenance.
Why This Matters: A well-designed lid means faster, safer filter changes—and when maintenance is easier, operators are far more likely to keep up with regular cleanings, reducing the risk of clogged filters and material flow issues.
Vacuum Sequencing Valve – Integrated vs. Remote
The vacuum sequencing valve, also known as the station valve, is what tells each receiver when it’s time to pull material from the central system. Think of it as a traffic signal for your conveying system—controlling the flow of vacuum and resin so that each receiver takes turns pulling material without causing a jam.
Here’s how it works:
- Without a sequencing valve, all receivers would try to pull material at the same time— dispersing available vacuum, overloading the system, and ultimately preventing material from flowing properly.
- With a sequencing valve, each receiver gets a precise, timed signal telling it when to activate, ensuring smooth, coordinated material flow.
Many traditional vacuum receivers require a separate, external sequencing valve, meaning:
- More parts to install → Extra wiring and setup time.
- Hard-to-reach components → If it’s mounted high, troubleshooting or repair becomes a hassle.
- More components to manage → Remote valves add system complexity by separating key functions from the receiver itself, making setup and future adjustments more involved.
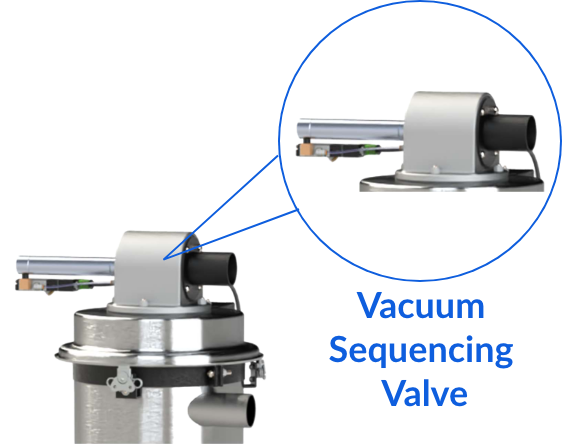
Some modern receivers integrate the sequencing valve directly into the receiver assembly, reducing installation time and simplifying operation.
Novatec’s VRX Series does just that—by incorporating the sequencing valve onto the receiver, it eliminates extra field wiring and makes installation seamless.
Why This Matters: Fewer components mean less time spent troubleshooting, lower installation costs, and a cleaner setup.
3. Filter System & Blowback Cleaning
A vacuum receiver’s filter system plays a crucial role in maintaining efficiency. If your filter clogs, airflow is restricted, material stops moving, and production slows down.
Receivers use different types of filters depending on the material—typically flat disk filters (sometimes called pellet screens) for standard pellets and regrind, or cartridge filters for dusty materials and powders.
Regardless of the filter type, one of the biggest factors affecting maintenance is whether the receiver has a blowback cleaning system.
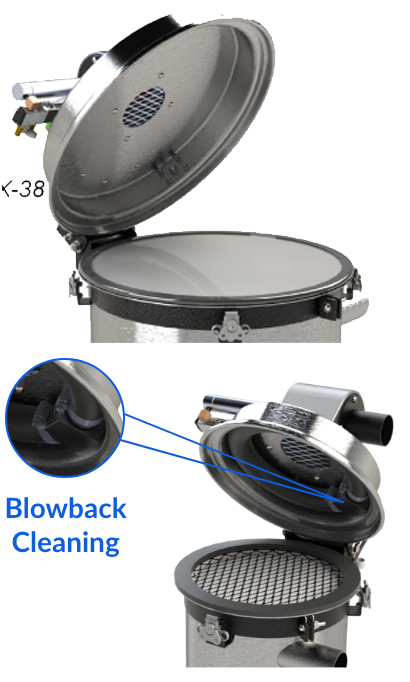
- Standard Receivers (No Blowback) – These rely entirely on manual filter cleaning. Effective for clean-running materials like virgin pellets and some regrind, but filters can clog quickly with dusty materials.
- Receivers with Blowback Cleaning – Use compressed air pulses after each loading cycle to automatically clear dust buildup, reducing the frequency of manual cleanings—especially important when handling dusty materials or powders. These pulses push the loosened dust back into the material stream so it can be conveyed downstream instead of accumulating inside the receiver.
Most processors don’t realize how quickly filters can clog—especially when handling dusty materials. That’s why many receivers can be supplied with some form of blowback system to keep filters clean.
- Novatec’s VR Series is offered with the option to have a blowback system to help remove dust after each conveying cycle. This feature is essential for processors handling dusty materials and regrinds, providing additional cleaning power and extending manual maintenance intervals.
- The VRX Series takes this a step further by offering its MicroBurst™ Blowback System, an optimized pulse-cleaning system that delivers stronger, more efficient filter cleaning, reducing maintenance and ensuring peak airflow for longer.
- For extreme cases—like handling fine powders—the VRP Series uses PTFE-coated, washable filters that prevent clogging altogether, and comes with filter blowback as standard.
Why This Matters: A well-designed filter system reduces maintenance time, improves efficiency, and keeps material moving smoothly.
4. Material Inlet & Cyclonic Flow Design
How material enters a receiver affects wear, fines generation, and efficiency. Poorly designed receivers cause material to slam into the receiver body, creating unnecessary dust and premature wear.
Some receivers use a tangential material inlet to create a cyclonic effect, allowing resin to enter smoothly without excessive impact, gently sliding along the inner wall of the chamber instead of directly impacting against it.
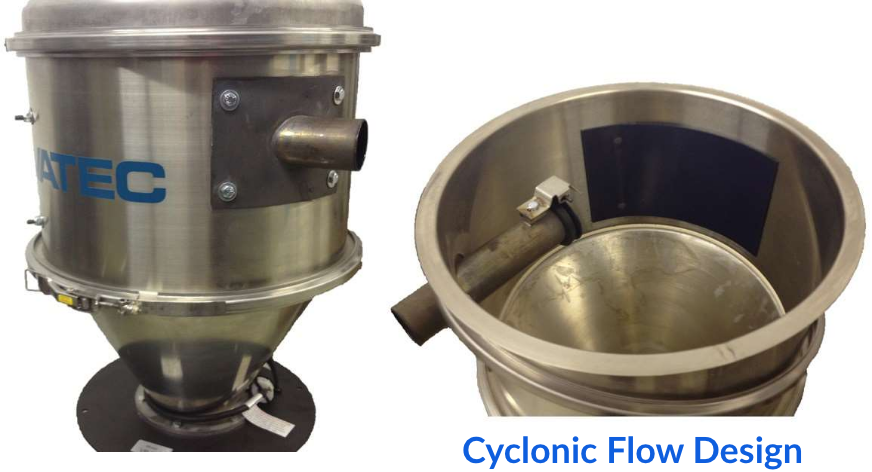
- Novatec’s VR, VRX, and VRP Series incorporate this design, reducing material degradation and minimizing dust generation inside the receiver.
- For powders, airflow control is even more critical. The VRP Series is designed to handle ultra-fine materials, ensuring better separation of fines and preventing material buildup inside the receiver.
Why This Matters: A cyclonic inlet design extends receiver lifespan, improves airflow, and reduces fines-related issues—which is especially important when dealing with dusty regrind and powders.
5. Discharge Valve – Gasketed vs. Standard
The discharge valve is where material exits the receiver and flows into the processing machine, but not all materials flow the same way—and that’s where discharge design becomes important.
- Pellets and free-flowing materials → Standard gravity flapper discharges with gaskets typically handle these materials well.
- Regrind and irregular shapes → These materials are more prone to bridging—a common issue where material stacks and clumps together at the discharge funnel or cone, blocking flow. In these cases, larger-diameter discharges or optional bridge breakers may be needed to keep material flowing smoothly.
- Fine powders → Powders have unique flow characteristics that sometimes require special handling techniques. While the discharge itself doesn’t typically change, more challenging powders—especially those prone to clumping—may benefit from larger discharges or bridge breaker options, similar to regrind applications.
A properly applied discharge design plays a critical role in ensuring reliable, consistent material flow. When a discharge isn’t suited to the material being conveyed, processors may experience:
- Inconsistent material flow—leading to overfeeding, underfeeding, or production interruptions.
- Bridging issues—especially when handling difficult regrind, fine powders, or sticky materials.
- System inefficiencies—forcing operators to intervene and clear blockages manually.
All Novatec vacuum receivers—VR, VRX, and VRP Series—utilize gasketed gravity flap discharges as standard. These are available in:
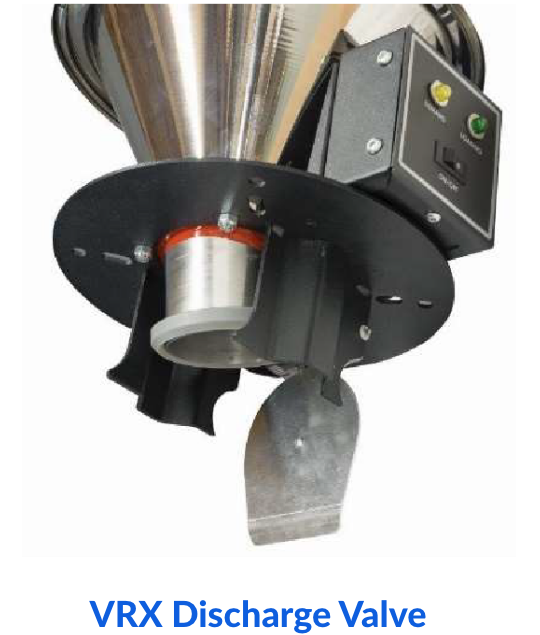
- 2-inch diameter – Standard on smaller receivers (5 to 19 lb capacity).
- 5-inch diameter – Standard on larger receivers (38 lb capacity and above), with optional availability for 12 and 19 lb models.
- 3-inch low-profile, shrouded discharge – Standard on VRX receivers with 12 to 30 lb capacity, with optional 5-inch versions for higher capacities.
Although all three series (VR, VRX, and VRP) share the same discharge options, the VRX incorporates a low-profile, shrouded design that enhances clearance for tight installations.
Why This Matters: Properly matched discharge designs—combined with the right diameter and optional flow aids like bridge breakers—help prevent bridging, improve flow consistency, and reduce the need for manual intervention, especially when handling difficult materials like regrind or fine powders.
4. Standard Receivers vs. Powder Receivers: What You Need to Know
Many processors don’t realize there’s a difference between standard and powder-specific receivers—until they start dealing with constant clogs, filter bypass, inconsistent flow, and excessive downtime.
Where Standard Receivers Work Best:
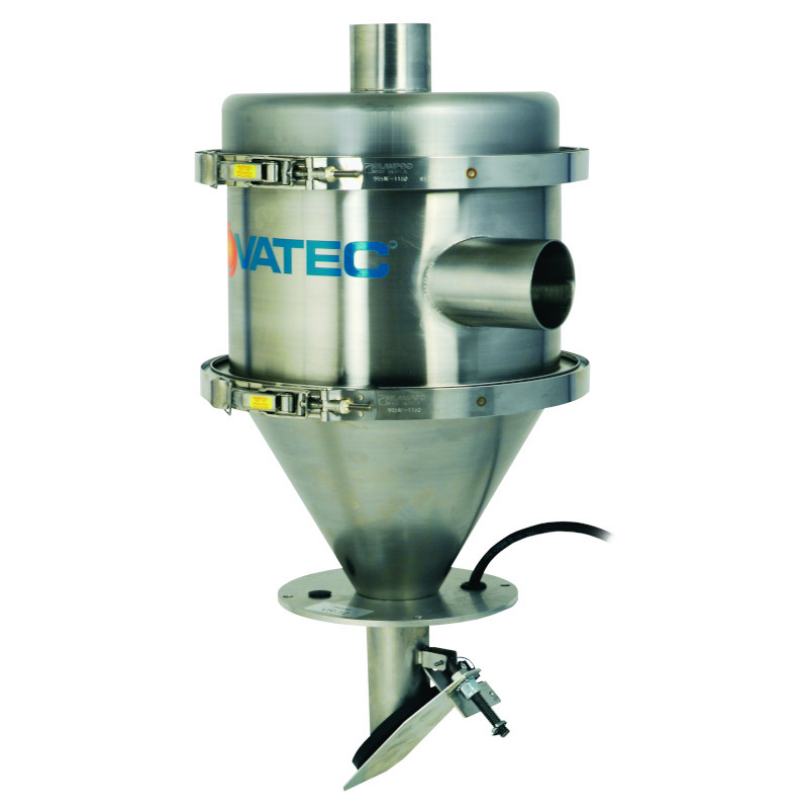
- Virgin pellets and general-purpose regrind
- Low-dust applications where standard filters work well
- Operations that don’t mind occasional manual filter cleaning (with or without the assistance of blowback cleaning)
But when handling powders, standard receivers often struggle:
- Filters clog too fast – Fine powders overwhelm standard filters quickly, leading to excessive fines and dust being pulled all the way to the vacuum pump, where they can cause premature wear and reduce system efficiency.
- Airflow gets restricted – If air can’t move properly, neither can the material.
- More manual cleaning = More downtime – Operators spend time maintaining equipment instead of running production.
This is where powder-specific receivers come into play.
How Powder-Specific Receivers Solve These Issues:
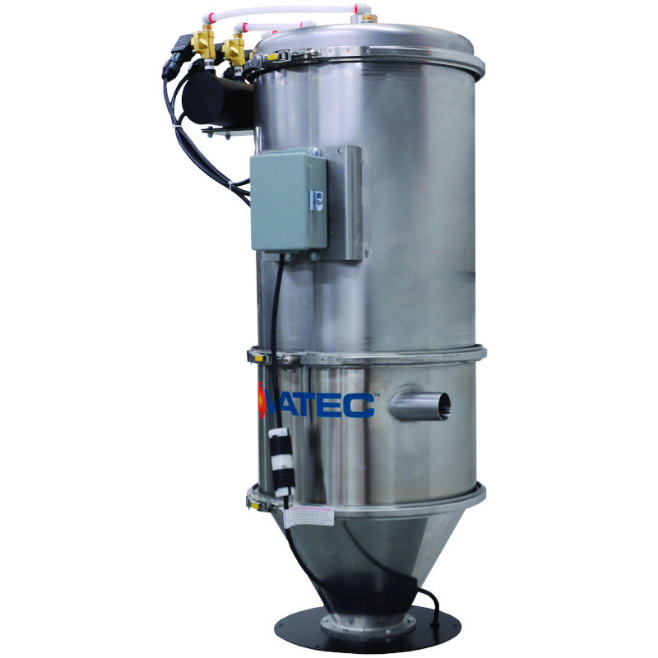
- Larger Filter Surface Area – Allows more airflow and prevents premature clogging.
- PTFE-Coated, Washable Filters – Designed to handle ultra-fine materials.
- Automatic Blowback Cleaning – A standard feature on powder receivers, it clears dust buildup regularly to reduce maintenance and keep filters working longer.
Some manufacturers offer basic filter upgrades for powders, but true powder-handling receivers—like Novatec’s VRP Series—are designed from the ground up for fine materials.
Why This Matters: If you regularly process powders, PVC, or high-dust materials, choosing a powder-optimized receiver can eliminate unnecessary downtime and maintenance headaches.
5. Novatec’s Vacuum Receiver Lineup: Which One is Right for You?
- VR Series – The Industry Workhorse
If you’ve been around plastics processing, you know the VR Series. It’s been a reliable staple in the industry for years—a go-to choice for processors who need a durable, time-tested vacuum receiver that gets the job done.
What makes it great?
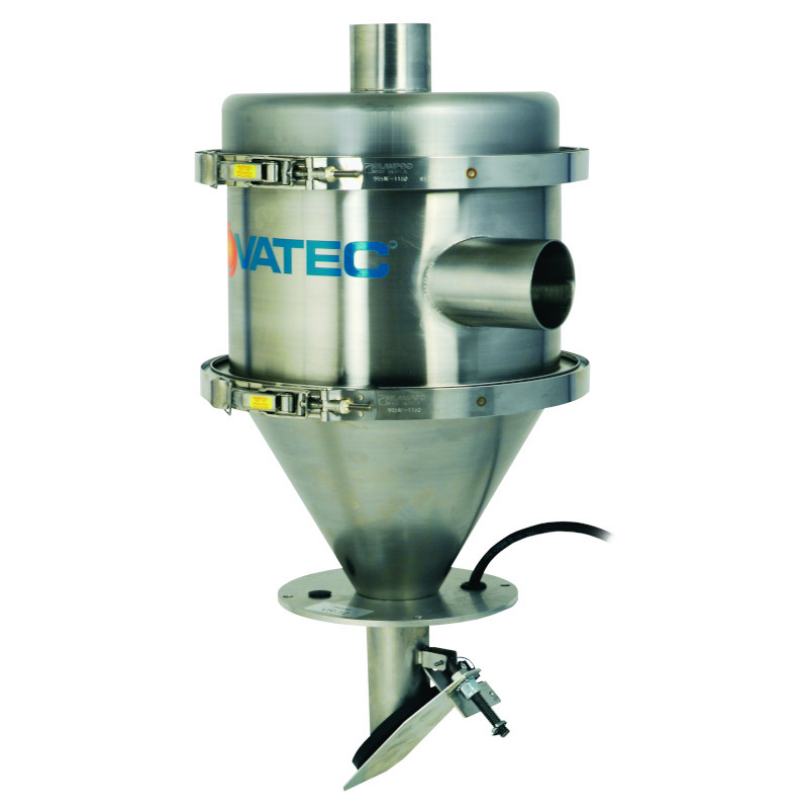
- Stainless steel body – Built to withstand years of operation, even in demanding environments.
- Modular design – Components can be swapped or expanded easily for long-term flexibility.
- Optional automated blowback system – Available to help maintain airflow by clearing dust from filters after each conveying cycle. Essential for dustier materials or operations aiming to reduce manual filter cleaning.
- Proven reliability – The VR Series has been an industry standard for decades, relied on by processors for its durability and consistent performance.
Considerations to keep in mind:
- Manual maintenance – The lid needs to be fully removed for filter changes, which can be difficult for high-mounted receivers.
- Requires separate installation of station valves – Meaning additional wiring and setup compared to receivers with integrated sequencing valves.
- Basic discharge design – Works well for pellets and general regrind, but it lacks the low-profile, space-saving design of Novatec’s VRX discharge, which offers improved accessibility and installation flexibility.
For processors with specialized needs, the VR Series can be configured with optional upgrades to enhance performance in challenging environments:
- Automated Filter Cleaning System – Optional pulsed air blowback system helps clear dust from filters after each conveying cycle, reducing manual cleaning needs for both standard and dustier materials.
- High-Wear Package – Replaceable ceramic-coated inlets, deflectors, and an impact plate to protect against abrasive materials.
- High-Heat Package – Upgraded gaskets that withstand temperatures up to 400°F, making it ideal for PET drying applications.
The VR Series is ideal for processors who want:
- A reliable, cost-effective receiver that delivers proven performance.
- A modular system that can be expanded or serviced easily.
- An optional automated filter cleaning system that can reduce manual filter maintenance for both standard and high-dust applications.
- A receiver designed for facilities that prefer a traditional, customizable setup.
For many processors, the VR Series is everything they need—a solid, durable receiver that’s been trusted for years.
But for those looking to simplify maintenance, speed up installation, and enhance performance even further—keep reading.
2. VRX Series – Vacuum Receivers Reimagined
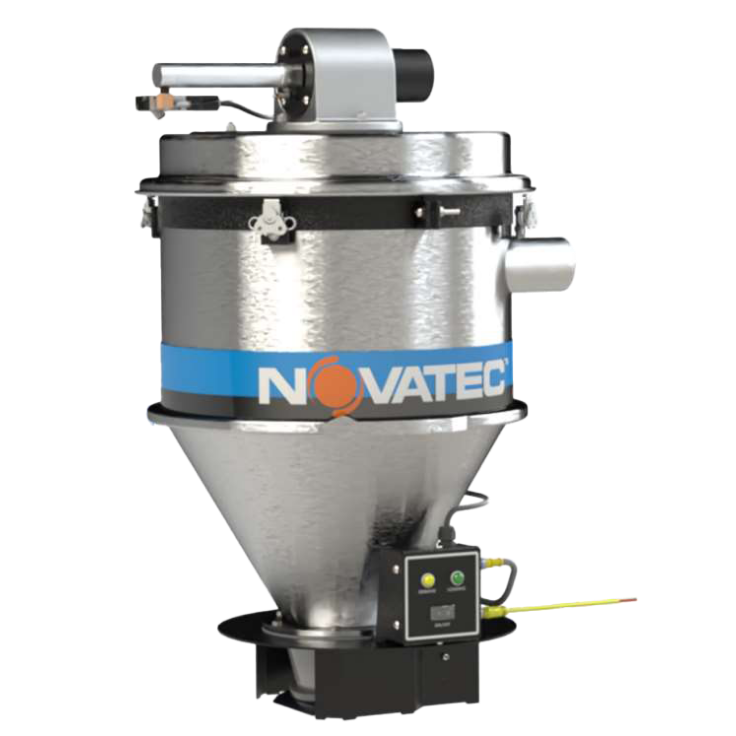
While it may seem like a premium upgrade, the real value of the VRX comes from what it replaces. With fewer components to install, less wiring to manage, and built-in design improvements that reduce downtime, many processors find that it delivers a lower total cost of ownership in the long run.
Easier to Install, Fewer Components to Manage
One of the biggest advantages of the VRX is that it eliminates the need for an external sequencing valve. With standard vacuum receivers, the sequencing valve is a separate component that has to be mounted and wired separately—often in difficult-to-reach places like overhead rafters. The VRX simplifies this by integrating the sequencing valve directly into the receiver lid, significantly reducing installation time and system complexity.
Beyond the sequencing valve, the VRX also consolidates all wiring into a single connection, eliminating the multiple cables required for a traditional receiver setup. With fewer components to install and maintain, processors can set up and expand their systems with far less hassle.
- Integrated Vacuum Sequence Valve – Eliminates separate valve installation and extra wiring thanks to its lid-mounted design.
- Single Wiring Connection – Fewer cables mean faster setup, fewer potential failure points, and a cleaner install.
Maintenance Made Simple
Routine maintenance is often delayed because it’s inconvenient or time-consuming. The VRX is designed to remove those obstacles, helping operators keep material flowing with minimal downtime.
The hinged lid makes filter changes fast and effortless, especially for high-mounted receivers, while the local on/off switch allows an individual receiver to be serviced without affecting the entire system.
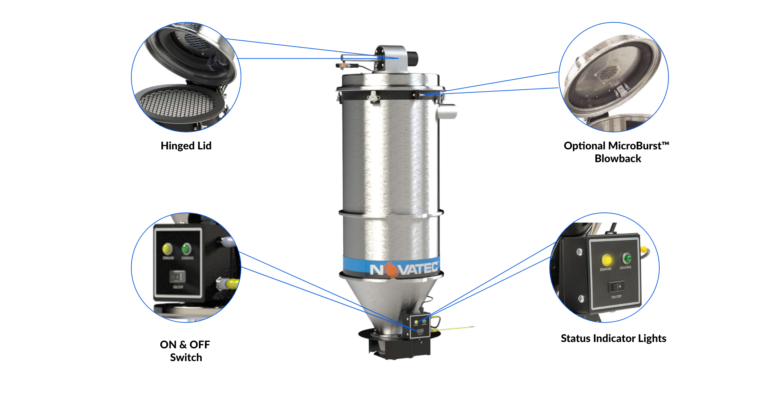
- Hinged Lid for Easy Access – No heavy lifting or disassembly required.
- Local On/Off Switch – Lets operators safely shut down a single receiver without affecting the rest of the system or having to access the central controller.
- Optional MicroBurst™ Blowback System – Optimized for more effective filter cleaning, reducing dust buildup and extending maintenance intervals.
- Status Indicator Lights – Help operators quickly identify issues without needing to check the control panel.
Like the VR, the VRX can also be customized with options like high-wear protection, high-heat gaskets for materials up to 400°F, and alternative blowback solutions for unique material challenges—offering flexibility for processors with specialized needs.
Why It May Cost Less Than You Think
On paper, the VRX might seem more expensive than a standard VR receiver, but that doesn’t tell the full story. With a traditional VR setup, you also need to purchase a separate sequencing valve, install extra wiring, and factor in additional labor. When you account for those extra costs, the price gap shrinks significantly—often making the VRX a more cost-effective choice in the long run.
For processors looking to simplify their system, reduce installation headaches, and minimize maintenance downtime, the VRX provides a solution that is both practical and forward-thinking.
3. VRP Series – Engineered for Powders & Dusty Materials
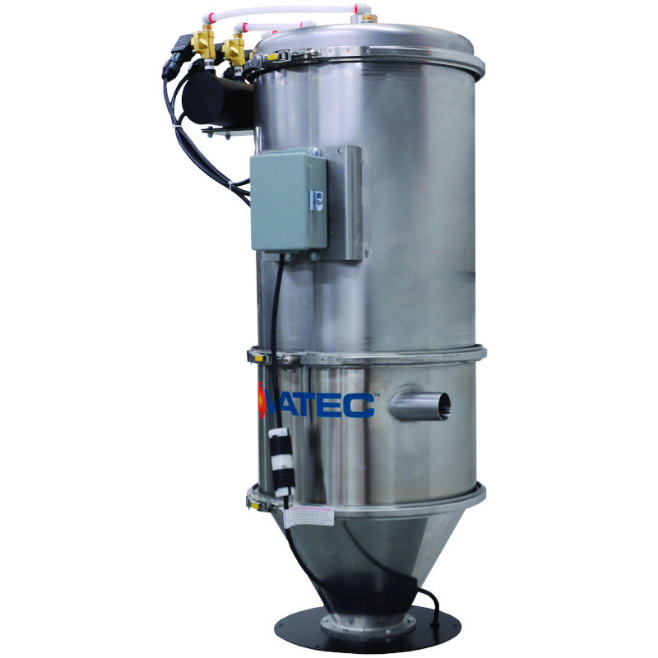
Handling powders in a vacuum conveying system presents unique challenges. Fine, lightweight materials like PVC, calcium carbonate, and titanium dioxide behave very differently from standard pellets or regrind. Without the right receiver design, powders can clog filters, cause dust buildup, and create inefficient material flow.
The VRP Series is specifically designed to handle these difficult materials, ensuring consistent flow, minimal maintenance, and longer system uptime.
How the VRP is Optimized for Powders:
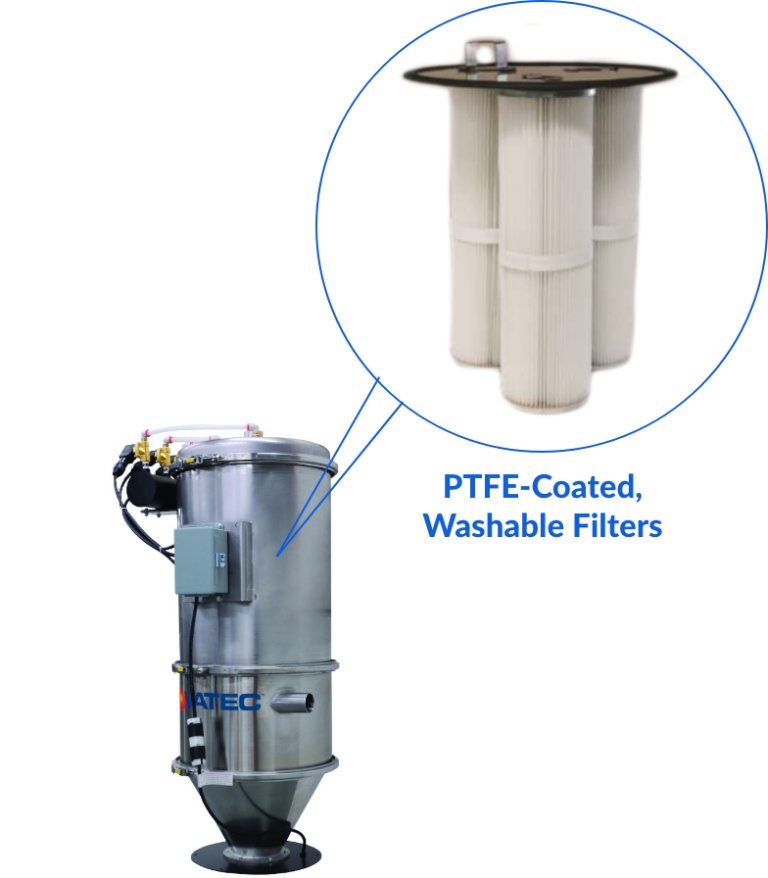
- PTFE-Coated, Washable Filters – Unlike traditional felt filters, PTFE-coated filters resist powder buildup, are washable, and last longer—reducing costly replacements
- Automatic Blowback System (Standard) – Fine powders can quickly clog filters, restricting airflow. The VRP’s automated blowback system comes standard, cleaning the filter after every cycle to keep airflow unrestricted and the receiver running smoothly.
- Specialized Filtration & Cleaning Focus – While the VRP shares the same overall body design as the VR, its filtration and standard blowback system are specifically selected to handle fine powders and dusty materials—ensuring more reliable performance and reduced manual maintenance.
For processors handling standard pellets or regrind, the VR or VRX may be the best choice. But for facilities regularly working with powders or dusty regrind, the VRP minimizes downtime, reduces manual filter cleaning, and helps maintain reliable material flow.
Custom Options to Fit Your Process
In addition to the standard and optional features covered for each model, Novatec offers a variety of shared enhancements across the VR, VRX, and VRP Series to match your specific process requirements. Available options include:
- Bridge breakers to prevent bridging and improve flow for challenging materials.
- Knife gate discharges for precise material control in specialized applications.
- Fill-to-level loading for batching applications or processes that require partial loading.
- And more — all designed to help you configure the perfect receiver setup for your plant.
6. Which Receiver Should You Choose?
- VR – The industry workhorse—a durable, cost-effective choice for processors who want a time-tested, modular solution that just works.
- VRX – Designed for efficiency—simplifies installation, minimizes maintenance, and optimizes material flow with smart, built-in upgrades.
- VRP – Engineered for powders—handles dusty, fine materials with ease, preventing filter clogs and keeping production running smoothly.
Final Thoughts: Finding the Right Fit for Your Operation
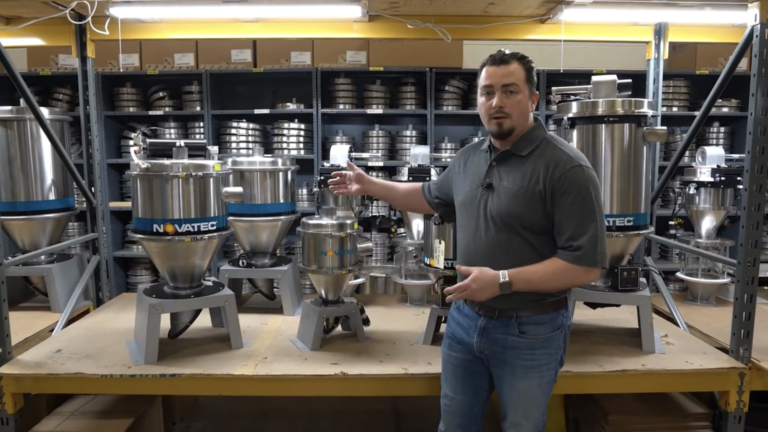
Vacuum receivers may not be the flashiest part of plastics processing, but they’re one of the most critical to keeping production running smoothly. Choosing the right one isn’t just about moving material—it’s about reducing downtime, improving efficiency, and making operations smoother for years to come.
Whether it’s the tried-and-true VR Series, the streamlined and maintenance-friendly VRX Series, or the powder-optimized VRP Series, selecting the best fit for your plant can have a significant impact on uptime and operating costs.
No matter the application, choosing the right receiver can make a big impact on uptime, efficiency, and long-term operating costs.
Still weighing your options? Drop us a line—no pressure, no sales pitch—just a conversation about what works best for your operation.
Because the right receiver isn’t just another piece of equipment—it’s the key to keeping material flowing, minimizing maintenance, and making your plant more efficient.
Let’s figure it out together!
Submit A Question: Conveying
Ask the Expert
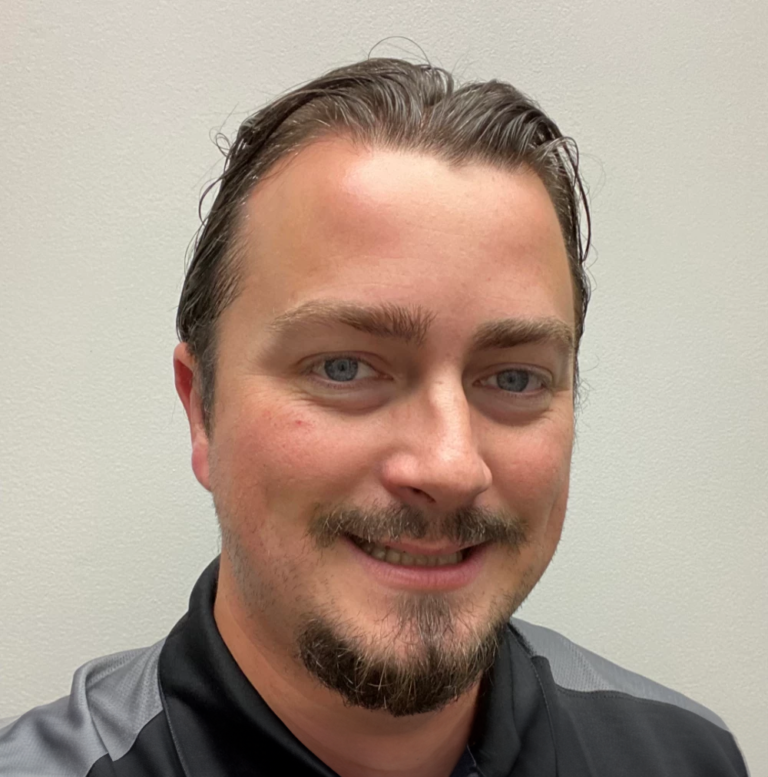