Question:
We produce spherical PET pellets. Most of our customers have systems designed for strand-cut pellets, which have a more square shape.
Can you help us evaluate the what the impact of switching from a strand-cut pellet to a spherical pellets would have from a conveying point of view?
Question:
What causes “Angel-Hair”?
Response:
Softer materials such as PE or PP are most likely to produce angel hair. Running material at a higher-than–necessary pickup velocity will exacerbate the problem because the pellets generate frictional heat as they pass through the conveying lines, especially when they travel through elbows. If the bulk density of your material is in the 36-38 lb/ft3 range, the pickup velocity should be around 3000’/minute. A bulk density of 50 lb./ft3 requires a pickup velocity of about 3500 ft/minute. If you are conveying something outside that range, see the attached formula to determine what the proper pickup velocity should be for your material. Remember that elbows should have a radius of 6-8 times the pipe diameter because tighter bends not only increase friction but increase pressure drop. You may also overcome the problem by installing elbows with rifling on the interior surface as they tend to make the pellets tumble instead of sliding around the curves. This reduces frictional heat.
Examples:
500 x √Material Bulk Density = Optimum Pickup Velocity
500 x √36 lb/ft3 = 500 x 6 = 3000 fpm
500 x √50 lb/ft3 = 500 x 7.07 = 3536 fpm
Question:
Is it better to have relatively empty lines between each demand or to keep the line
full. Which one is likely to create less angel hair?
Response:
In general, it is better to keep the lines fairly full, as long as you don’t overload the lines
to the point where line plugs occur. Operating the pumps at designed operating vacuum is
optimal for velocity profile. If this operating point creates too much velocity, and a reduction
in conveying rate will not starve the process, a reduction in speed and airflow can be used to
reduce velocity and operating vacuum. When purging or emptying the lines, speed will actually
increase as the lines empty, so this would tend to create more problems over time than a filled
line.
Question:
How important is pellet temperature for generating fines/angel hairs?
Response:
Softer pellets or pellets with a low melt index are more subject to softening by high
conveying temperatures, which is likely to create angel hair.
Question:
Don’t High-Vacuum pump (smaller diameter pipe) create more angel hair? Why not?
Response:
They would create more angel hair on softer materials if velocity control were not employed. Another advantage of velocity control is that it actually increases throughput.
Question:
Could you tell us how to determine the diameter of resin conveying pipe?
Response: Generally, the equivalent feet, material density and throughput requirements are used to
develop the proper pump size and the material lines are matched to the pump.
Question:
How can we reduce angel hair and or dust from railcar to silo and silo to machine?
Response:
The best way to minimize dust and angel hair while moving material in and out of silos is to reduce pump speed and vacuum level. You can also create controlled leaking to obtain optimal airflow for conveying.
Question:
Are angel hair problems reduced in sub-zero temperature conditions associated with winter weather?
Response:
Angel-hair problems depend on the polymer and the velocity, although the problems tend to be minimized in colder weather.
Question:
Are elbow upgrades effective in reducing angel hair? Are they available in sizes to retrofit to existing equipment?
Response: Yes, elbow upgrades are generally effective in reducing angel hair problems. You have a choice of special elbow designs, with sizes to match conveying pipe diameters. Hard elbows with material pockets are most effective, though they may create added system resistance. The least expensive choices are spiral grooved or shot peened tubing, though minimum wall thickness is 14 gauge, so transition segments may be necessary to fit the conveying line size.
Question:
Where is the best place in a conveying system to check for formation of angel hair and fines?
Response:
Generally, angel hair will form in the piping. You may see it in the form of a skin that builds inside the tube surface, especially in elbows. Elbows closest to the destination are most susceptible. If angel hair is forming, it will likely appear at destination receivers and storage bins or hoppers, where it can form a blockage and starve the end process. It can also create plugged receiver screens, but it rarely continues to the system final filter. You can place easily accessible angel hair traps in the material conveying lines. The traps utilize a coarse metal mesh that allows pellets to flow to the process, but holds angel hair for regular removal.
Question:
How does velocity of conveying affect fines generation from a railcar to a silo?
Response:
Typically, the carrier or the person responsible for unloading material into a silo wants to
get the job done at the highest velocity possible. That may create fines or angel hair. It’s best to
determine what unloading speed is right for each material and make sure delivery personnel act
accordingly.
Question:
How does the conveying temperature affect dust generation in brittle polymers?
Response:
Fines generation is affected more by the polymer type and the velocity than by temperature.
Question:
Regarding angel hair formation: If the only knob we can turn is the quantity of pellets we put in our pull/push system, should we move toward fewer pellets at higher velocity or more pellets at lower velocity?
Response:
Generally, it is better to move more pellets at a lower velocity, as long as you don’t
overload the system and create line plugs. Also, look into special elbows, including rifled tubing.
Thank you to all for your questions.
Conveying questions can be answered by Novatec experts
Ask the Expert
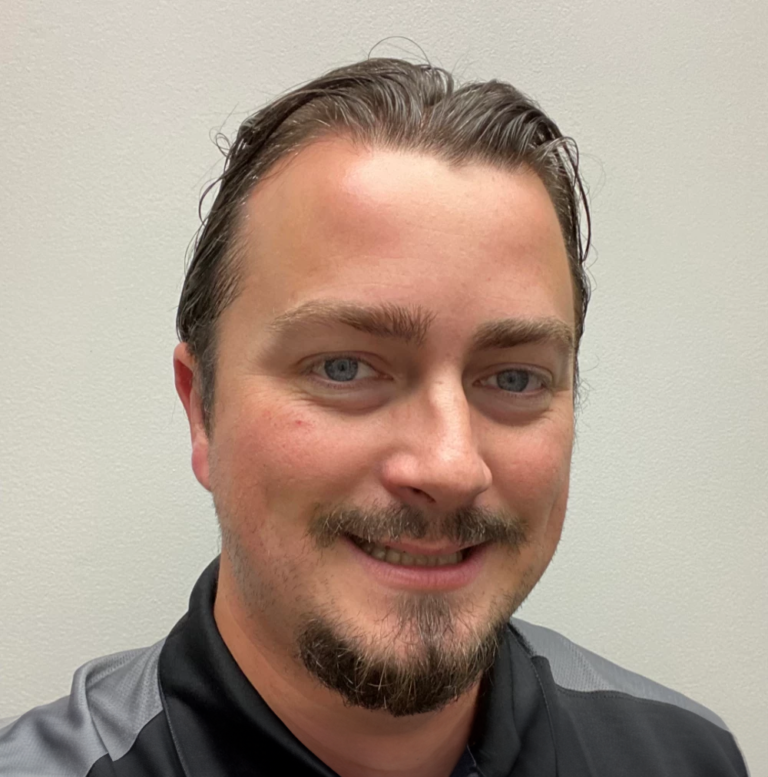