Menu
Let’s look at the ramifications of not having a central system – and think about the associated costs – can you estimate your yearly losses from these problems?
It is not unusual to discover tens of thousands – even hundreds of thousands of wasted dollars in a plant without a good centralized resin handling system.
PROBLEMS = LOST PRODUCTION TIME, LOST PROFITS AND LOST CUSTOMERS!
Problems Experienced Without a Central System:
- Space needed for plant consolidation
– If you can’t handle more process machines some other plant will - Congestion on the floor around machines
– Slows workers – increases spillage and chance of injury - Lack of material validation/verification
– Can’t bid on contracts where validation required - Wrong material going to wrong machine
– Lost production time, rejects and lost material - High material spillage
– Loss of material and labor + safety hazard - Material related part defects
– Producing scrap instead of saleable parts - High maintenance/labor costs
– Increased payroll and parts cost - Frequent material changes
– Lost production time - Inefficient work flow
– Wastes space and labor - Lack of Automation
– Adds labor costs and extends lead times - Constrained production capacity
– Can’t increase revenue - Lengthy hopper cleanout times
– Increased labor – lost production - Poor drying of material
– Rejected parts – lost customers
Usually, the cost to install or upgrade an efficient resin handling system is recovered in a matter of months – not years – See examples of central system paybacks. Investment payback in Months – Not Years but a review of conditions in your plant is required to identify areas of loss and possible remedies.
Ask the Expert
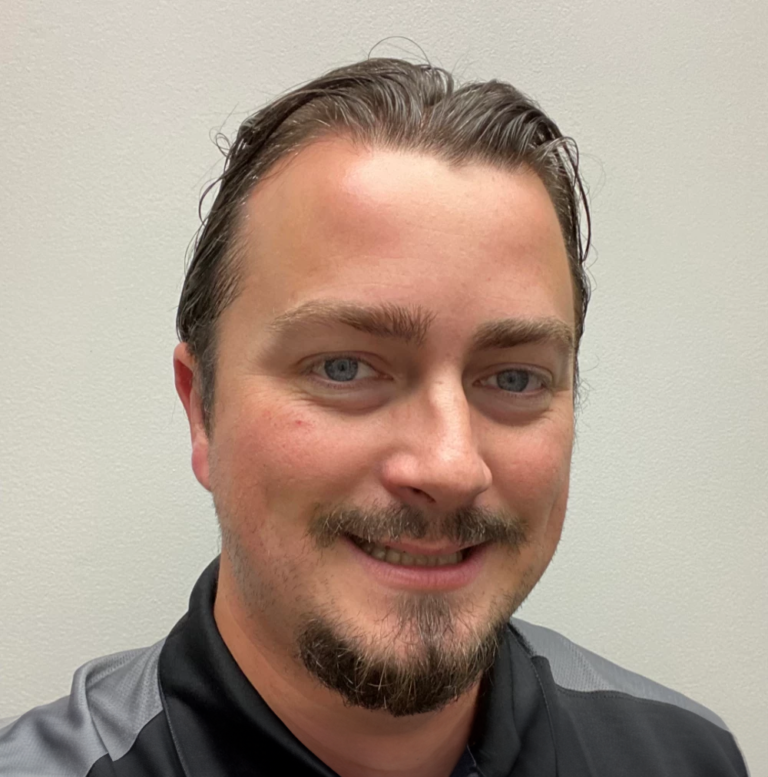