The Ultimate Guide to Vacuum Pumps for Plastics Processing: How to Choose the Right One for Your Plant
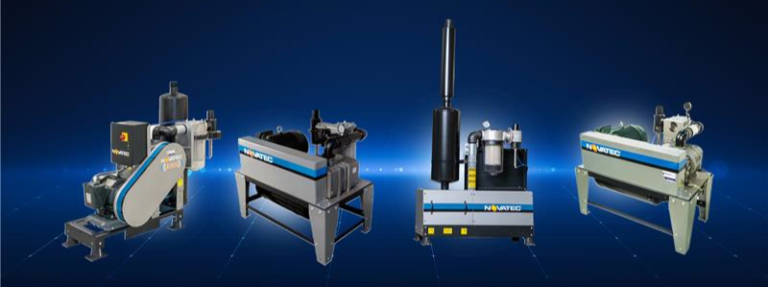
Vacuum pumps might not be the first thing on your mind—but choosing the wrong one can cost you. A pump that’s too weak leaves machines starving for material. One that’s too powerful can damage resin, waste energy, and drive up maintenance costs.
This guide is built to help you cut through the noise (literally) and find the right pump for your operation—whether you’re replacing an old system, troubleshooting performance issues, or making sure you’re not overspending on equipment you don’t need.
So grab yourself a coffee and let’s dive in.
1. Why Vacuum Pumps Are the Last Thing You Think About—Until They Stop Working
Vacuum pumps don’t get much love in plastics processing. Nobody stops in the middle of a shift to admire their performance. But when they fail, they’re all anyone thinks about.
A bad pump—or the wrong pump for the job—can derail your entire operation by:
- Slow or inefficient material flow – Your machines starve, productivity tanks.
- Clogging and plugging issues – Nothing kills a shift faster than a jammed-up line.
- High energy bills – Some pumps guzzle power like a ‘70s muscle car.
- Noise and compliance headaches – Loud pumps can trigger OSHA-mandated sound enclosures or ear protection, adding costs and frustration.
- Material damage and dust creation – Brute-force vacuum systems can slam materials into elbows, creating angel hair, dust, and even pipe blowouts.
But get the right pump, and suddenly:
- Your materials move faster and smoother.
- You save on energy, maintenance, and replacement parts.
- Your operators stop cursing at broken-down systems and deafening pump noise.
But there’s one factor that can turn even the right pump into a major headache—noise. And it’s not just about comfort. Excessive vacuum pump noise can bring OSHA compliance issues, legal risks, and even productivity problems to your operation.
2. The Hidden Cost of Loud Vacuum Pumps: OSHA Fines, Lawsuits & Hearing Loss
Vacuum pumps don’t just move material—they move air loudly. If your pump is too noisy, it’s not just an annoyance—it’s a compliance risk, a legal liability, and a financial drain on your operation.

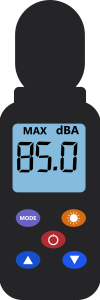
OSHA sets strict noise exposure limits to protect workers from hearing loss, and vacuum pumps can easily push these thresholds. If noise levels hit 85 dB(A) for an 8-hour shift, you’re legally required to implement a hearing conservation program, including annual hearing tests. 90 dB(A)? Hearing protection becomes mandatory. Over 115 dB(A)? Immediate protection is required—unprotected exposure is illegal.
And failing to comply? That can mean steep fines, forced retrofits, and increased regulatory oversight—but that’s just the beginning.
Hearing loss is a compensable injury in all 50 states. That means if your vacuum pump’s noise levels even flirt with OSHA limits, an affected employee has a strong case for legal action. And guess what? Lawyers are hunting for these cases.
You’ve probably seen the ads—TV commercials, online banners, billboards—offering legal representation for workplace hearing loss. These firms know that many plants operate right at OSHA’s noise limits, making them easy targets for lawsuits and worker’s comp claims.
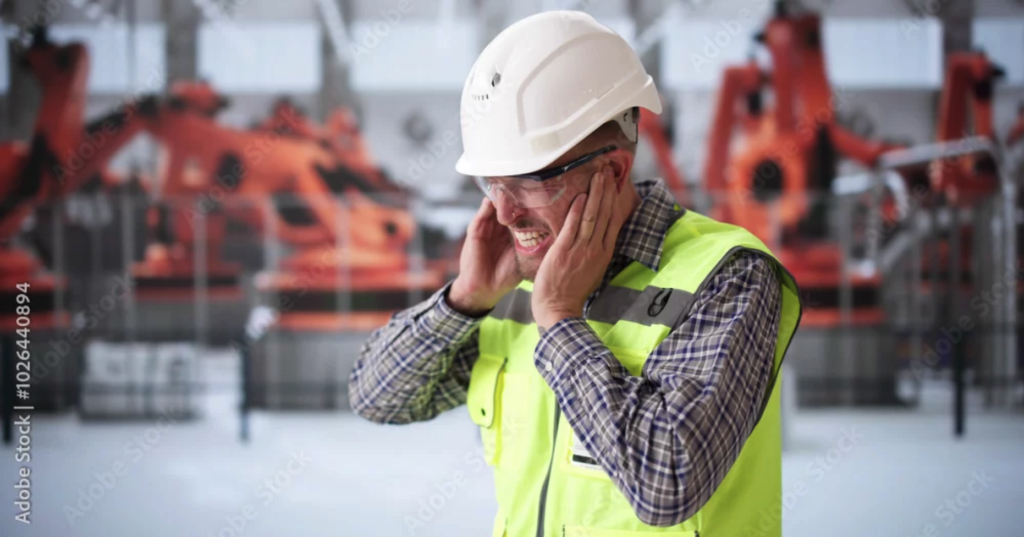
Sure, maybe your employee’s hearing loss came from blasting headphones or years of rock concerts. But if your vacuum pumps are running on the edge of compliance—or sometimes veer over—the liability is on you.
And the costs don’t stop there. If your pumps are too loud, you may be forced to:
• Install expensive sound enclosures
• Move pumps to a separate room (which often reduces efficiency due to longer piping runs)
• Deal with frustrated employees struggling with constant noise fatigue and miscommunication
So before choosing a vacuum pump, make sure you understand its noise levels and what they mean for your operation. Does it require hearing protection? Will it need sound enclosures? Can it run on the production floor without compliance headaches?
And the costs don’t stop there. If your pumps are too loud, you may be forced to:
- Install expensive sound enclosures
- Move pumps to a separate room (which often reduces efficiency due to longer piping runs)
- Deal with frustrated employees struggling with constant noise fatigue and miscommunication
So before choosing a vacuum pump, make sure you understand its noise levels and what they mean for your operation. Does it require hearing protection? Will it need sound enclosures? Can it run on the production floor without compliance headaches?
But noise isn’t the only factor in choosing the right vacuum pump. Efficiency, conveying distance, material protection, and long-term costs all play a role in finding the right fit. Let’s break down the options so you can make the best choice for your plant.
3. The Lineup: Finding the Perfect Fit for Your Plant
Choosing a vacuum pump isn’t a one-size-fits-all decision. Some processors need a simple, everyday workhorse. Others need a quieter solution or something built for long-distance conveying.
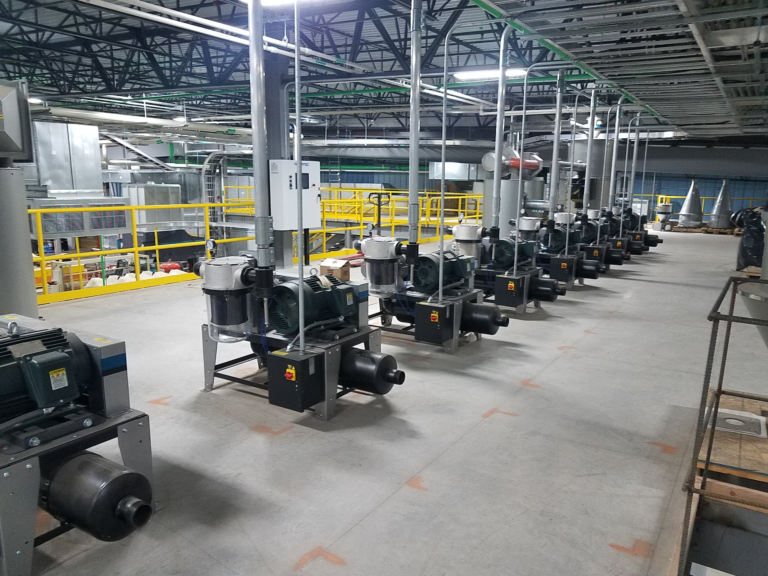
But here’s the catch—some manufacturers only offer a limited selection, which means you might be pushed into a pump that fits their lineup, not your needs. That’s why it’s important to know your options before making a decision. Let’s break them down.
Regenerative Pumps: A Niche Solution with High-Velocity Risks
Best for: Short-to-moderate distance (up to 350–600 equivalent feet) conveying and small-scale operations.
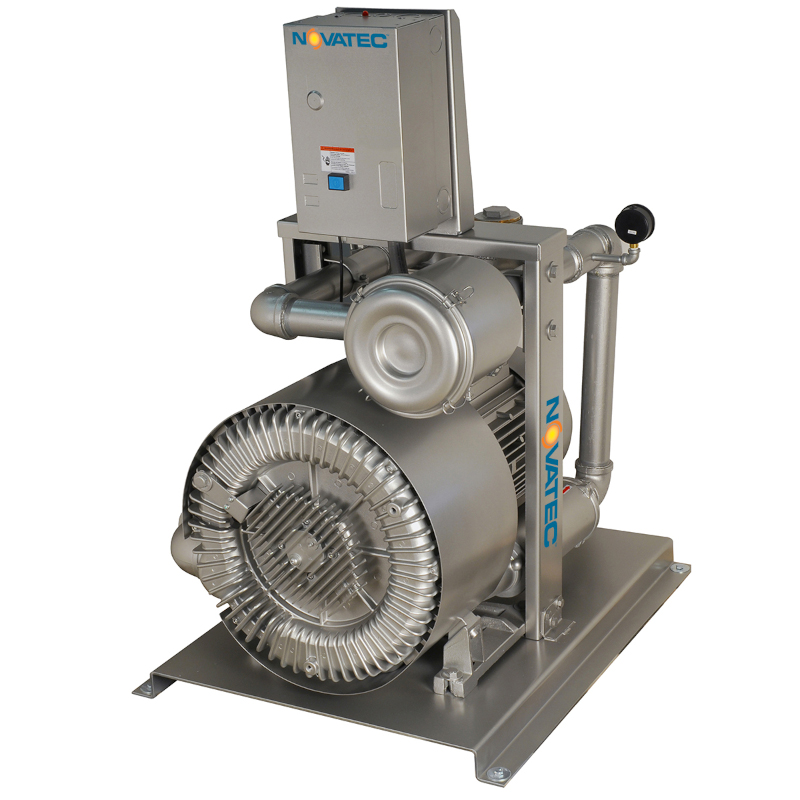
Regenerative (regen) pumps are compact, low-maintenance, and often operate at reasonably safe levels (74-81 dB(A)) without sound reduction packages. Their simple motor/fan design makes them a common choice in European factories, where short-distance conveying is typically the norm. While most regen pumps are best suited for short-distances, dual-stage models can extend that range into moderate-distance conveying (up to 600 equivalent feet).
For certain small-scale applications, regen pumps can be a practical solution. Medical parts processors working with small batch sizes in a cleanroom environment, for example, may benefit from a regen pump for short-to-moderate distance conveying.
- Small Footprint – Ideal for space-constrained setups.
- Lower Maintenance – Few moving parts mean minimal upkeep.
- Quiet Operation – Often meets OSHA noise compliance without requiring additional soundproofing.
But for the majority of plastics processors, regen pumps introduce serious challenges—particularly excessive velocity.
Unlike Positive Displacement (PD) pumps, which generate vacuum through mechanical compression, regen pumps rely entirely on high-speed airflow to create suction. As a result, they easily operate at roughly 10-15% higher velocity than generic PD pumps.
Velocity is one of the leading causes of problems in a conveying system. Excessive speed leads to material degradation, dust generation, equipment wear, and system failures.
Here’s why that matters:
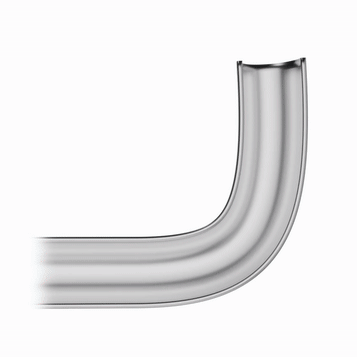
- Resin Degradation & Dust Generation – Higher resin can overheat and shear heat-sensitive pellets and increase impact forces on brittle resins. Ignoring this leads to angel hair, streamers, and/or fines that reduce material quality and clog filters.
- Plugging & Line Build-Up – The high-speed turbulence from regen pumps causes heat-sensitive or tacky materials to stick, collect, and clog in elbows and piping, leading to system shutdowns.
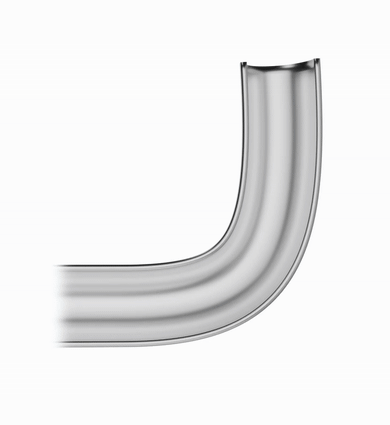
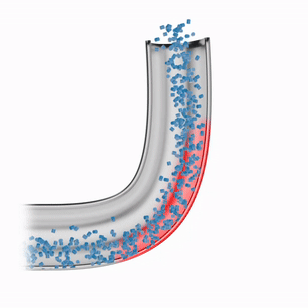
- Elbow Wear & Equipment Damage – Increased impact and sliding velocity of abrasive resin accelerates wear on elbows, piping, and vacuum receivers, leading to costly repairs and unplanned downtime.
- Elbow Wear & Equipment Damage – Increased impact and sliding velocity of abrasive resin accelerates wear on elbows, piping, and vacuum receivers, leading to costly repairs and unplanned downtime.
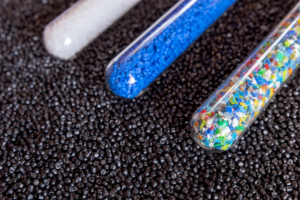
Some manufacturers attempt to compensate for regen pump limitations by offering “hybrid” regen pumps, marketing them as a quieter alternative to PD pumps. But these designs don’t solve the core problem— velocity is still too high, and the risks of resin degradation, plugging, and system wear remain. While some hybrid regen pumps can be paired with Variable Frequency Drives (VFDs) to reduce velocity, this often comes at the expense of throughput, pickup performance, and motor efficiency.
For processors handling longer distances, high-throughput materials, or fragile engineered resins, PD pumps provide a far more reliable and efficient solution in dilute conveying applications.
Positive Displacement (PD) Pumps: The Smart Choice for Any Application
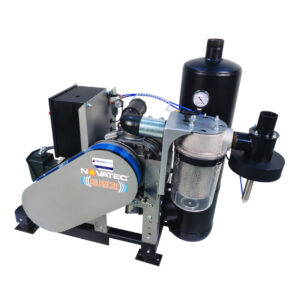
Best for: Standard to high-volume conveying, moderate to long-distance runs, and energy-efficient operation. Rated up to 750-1000 equivalent feet, depending on model.
If regenerative pumps struggle with velocity and wear issues, Positive Displacement (PD) pumps are the workhorses of the plastics industry—delivering stable, powerful conveying with superior efficiency.
Most manufacturers offer just one type of PD pump. If that one-size-fits-all model doesn’t match your operation’s needs, you’re left with two bad choices: settling for a misfit pump or being pushed into an expensive claw pump that you may not actually need.
At Novatec, we take a different approach. Instead of offering a single PD pump, we provide a full lineup of PD technologies—each engineered to optimize performance based on your specific processing needs, whether it’s balancing noise reduction, maximizing conveying efficiency, or tackling long-distance runs.
Let’s break them down.
1. VPDB Series – The Standard Workhorse
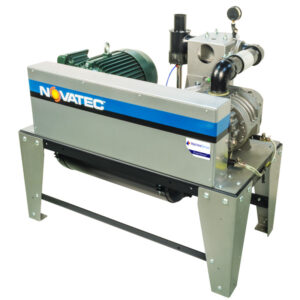
✔️ Reliable, cost-effective PD performance via traditional bi-lobe design
✔️ Built for consistent, everyday conveying needs
✔️ Rated for up to 750 equivalent feet
✔️ Sound Level: 83-89 dB(A) (can be reduced by 10-12 dB(A) with optional sound curtain kit)
For many processors, the VPDB Series is the go-to PD pump. It provides dependable performance for standard conveying applications while delivering superior efficiency compared to regenerative pumps. Unlike regen systems that degrade material with excessive velocity, PD pumps like the VPDB maintain optimal speeds to protect resin quality.
However, standard PD pumps—even efficient ones—can still create noise concerns. While an optional sound curtain kit can slash noise levels by a whopping 10-12 dB(A), this approach comes with some trade-offs—including additional cost, installation requirements, increased heat generation, and reduced visibility of pump indicators. Luckily there’s an even smarter solution. That’s where our SVP Series comes in.
2. SVP Series – The Quiet Performer
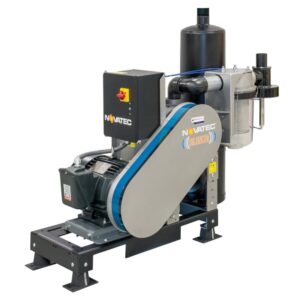
✔️ VPDB performance—but with enhanced noise reduction
✔️ Built-in sound-abatement components deliver PD performance with regen sound levels
✔️ Sound Level: 78-80 dB(A)
✔️ Ideal for processors who need OSHA-compliant, low-noise operations
We understand that vacuum pump noise is one of the biggest operational headaches in plastics processing. Traditional PD pumps can run loud, leading to OSHA compliance issues and the need for costly soundproofing.
That’s why we engineered the SVP Series—to deliver the same powerful performance as the VPDB, but with a meticulously designed integrated sound abatement package that eliminates the extra cost, installation, and maintenance challenges of an add-on sound curtain kit.
Why This Matters: If you’re already considering OSHA-mandated hearing conservation programs, choosing a quieter PD pump from the start can save you thousands in compliance costs while improving the work environment for your employees—without the added hassle of enclosures, cooling fans, or reduced pump visibility.
3️. MVP Series – The High-Powered Long-Distance Solution
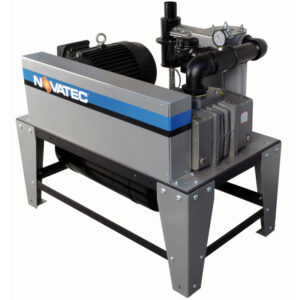
✔️ Designed for higher vacuum, longer distances, and heavy material loads
✔️ Handles up to 1000 equivalent feet without stepping up to a claw pump
✔️ Spiral flow design creates deeper vacuum levels than standard PD pumps
✔️ Sound Level: 83-90 dB(A) (can be reduced by 10-12 dB(A) with optional sound-curtain kit)
A common misconception is that moving material beyond 750 equivalent feet requires a claw pump. That’s not true.
The MVP Series bridges the gap between standard PD performance and ultra-long-distance conveying, delivering up to 1000 equivalent feet of powerful suction—without the steep cost jump of a claw pump.
And for processors concerned about noise? The MVP Series can also be equipped with the same sound curtain kit available for our VPDB models that reduces noise levels by 10 – 12 dB(A).
It’s everything you need to move materials over long distances without breaking the bank on claw technology.
4️. Infinity Series – The Ultimate Advancement in PD Pumps
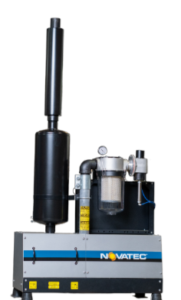
✔️ Reliable, cost-effective PD performance via traditional bi-lobe design
✔️ Built for consistent, everyday conveying needs
✔️ Rated for up to 750 equivalent feet
✔️ Sound Level: 83-89 dB(A) (can be reduced by 10-12 dB(A) with optional sound curtain kit)
Most processors think that if they need quiet operation, their only options are to settle for a regen pump or isolate their PD pump in a remote soundproof room—but that’s no longer the case. The Infinity Series is the quietest PD pump available today, so quiet that it can be placed right on the production floor—eliminating the need for costly sound enclosures or distant pump rooms. By keeping the pump on the floor, where it’s needed, you avoid the expensive, labor-intensive installation of long-distance piping required for remote setups—saving thousands on labor, infrastructure, and material costs.
With shorter conveying lines, you don’t have to overcompensate with a larger, high-powered pump just to cover extra distance, reducing both upfront equipment costs and long-term energy consumption. And because the Infinity Series can always be in sight, routine monitoring becomes effortless. Unlike pumps hidden in back rooms where issues can go unnoticed, built-in health indicator lights provide at-a-glance status updates, allowing for easy, proactive maintenance.
At the heart of the Infinity Series is the InfinityDrive Magnetic Motor, an innovation born from high-performance electric vehicle technology. Unlike traditional pumps that rely on belts and sheaves, this motor eliminates those failure-prone components entirely, using a direct-drive coupling for unmatched reliability.

No Belts, No Sheaves, No Hassle – Traditional belt-driven motors lose efficiency over time, require frequent adjustments, and are a major failure point. The InfinityDrive removes these entirely.
Ultra-Reliable Direct Drive – The motor is directly coupled to the blower, reducing vibration, increasing efficiency, and eliminating wear-prone components.
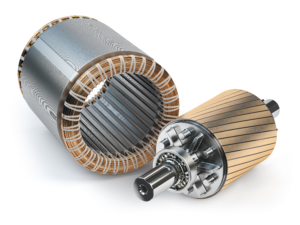
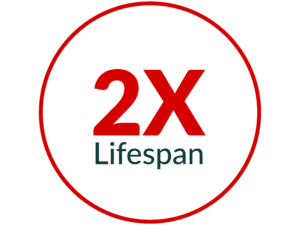
Double the Motor Lifespan – With fewer moving parts and reduced mechanical strain, the InfinityDrive lasts twice as long as traditional PD pump motors.
Smart Monitoring with PumpSense – Standard on the Infinity Series, PumpSense tracks system health and sends proactive maintenance alerts via text and email—preventing costly downtime. (Optional add-on for other Novatec PD pumps.)
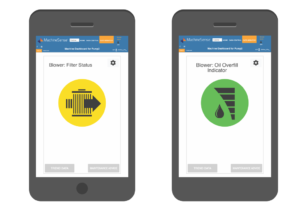
Energy efficiency is another game-changing aspect. Unlike conventional pumps that maintain high power draw even when idle, the Infinity Series dynamically adjusts energy usage based on demand.
Massive Energy Savings – Up to 7.5X more efficient in idle mode and 2X more efficient in operation than traditional PD pumps, significantly lowering electricity costs.
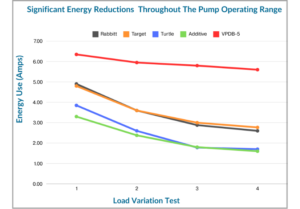
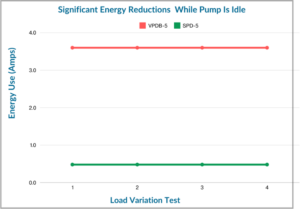
Modulates Power to Demand – The system never pulls more power than needed, preventing unnecessary energy draw and reducing system strain.
When paired with the FX3 Controller, the Infinity Series unlocks unprecedented precision. Users can fine-tune pump speed to match their materials, optimizing performance while safeguarding resins and equipment.
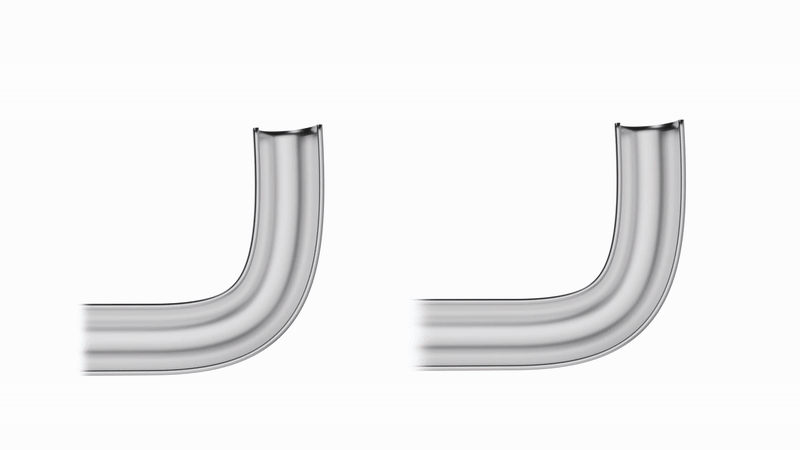
Unmatched Operational Range (35%–150% Capacity) – No other pump on the market offers this level of flexibility, with selectable settings to ensure gentle precision for fragile and abrasive materials.
Safeguards Resins, Equipment & Lines from Damage – Minimizes streamers, angel hair, and dusting while reducing wear on piping and components to extend system lifespan.
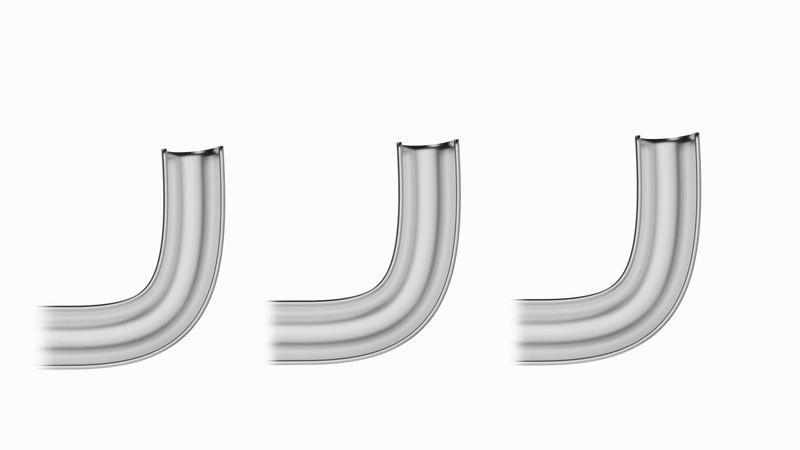
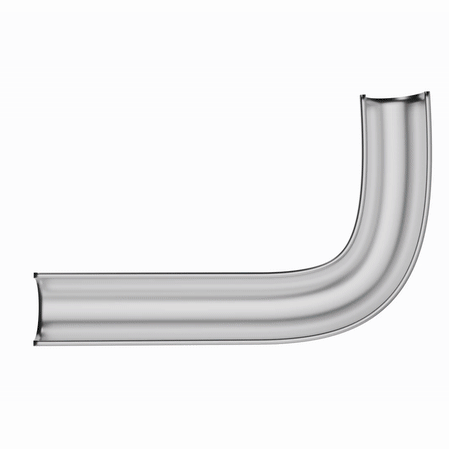
Automatic Blockage Clearing – Detects obstructions and delivers a short, controlled burst of power at 150% capacity to instantly clear the line—before it causes downtime.
The Bottom Line: Instead of trying to “hybridize” regen pumps (which still suffer from high-velocity issues), we advanced PD technology—eliminating its traditional drawbacks and pushing its capabilities further. With the Infinity Series we’ve simply made it quieter, more efficient, and longer-lasting than ever before—while effectively mitigating velocity-related material degradation.
Long-Distance Pumps: Do You Really Need a Claw Pump?
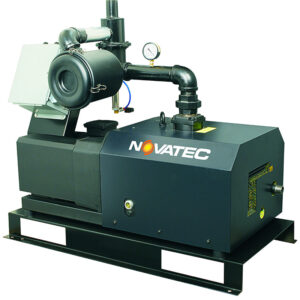
Best for: Extreme distances (above 1000 equivalent feet), ultra-high-volume conveying, and specialty applications.
Many processors assume that if they need longer conveying distances, they must upgrade to a claw pump. That’s exactly what some manufacturers want you to believe.
Here’s the reality:
- If your conveying distance is under 1000 equivalent feet, a properly selected PD pump (like the MVP Series) is almost always the more cost-effective solution.
- Claw pumps are powerful—but expensive compared to other vacuum pump technologies.
- If your system design is inefficient, a claw pump might brute-force a solution, but it won’t fix the root cause.
So when does a claw pump make sense?
- When your conveying distances exceed 1000 equivalent feet, and even a high-powered PD pump isn’t enough.
- When you need ultra-high vacuum levels for moving dense or heavy materials across extreme distances.
For these cases, the UVP Series Claw Pump delivers exceptional power and efficiency for extreme-distance conveying. With direct-drive operation, electronic motor overload protection, and minimal required maintenance, the UVP ensures high-performance material movement without excessive upkeep.
That’s why we only recommend claw pumps when they are truly required—not as a default option. If your system can be optimized with a PD pump, we’ll make sure you don’t overspend on technology you don’t need.
4. The Right Vacuum Pump for Your Plant
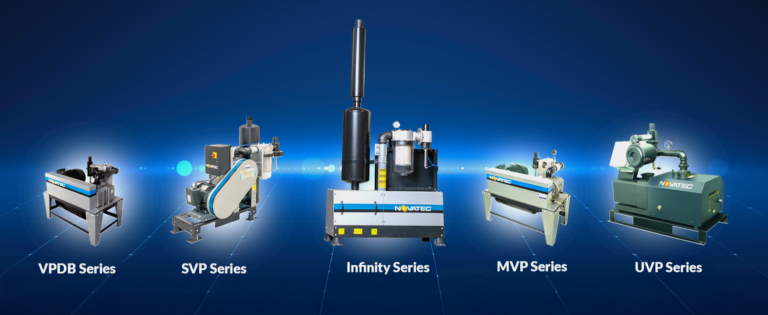
Different applications call for different vacuum pump technologies. Here’s a quick way to match the right pump to your operation:
- Short-to-moderate distance conveying (up to 350-600 equivalent feet), small throughput volume, in a cleanroom with small batch sizes? → A regen pump may be a viable option.
- Standard conveying applications requiring reliable, everyday PD performance? → VPDB Series
- Need to reduce noise while maintaining PD performance? → SVP Series
- Moving material over longer distances (750-1000 equivalent feet) or higher throughputs, but want to avoid the cost of a claw pump? → MVP Series
- Looking for the ultimate advancement in PD technology—ultra-quiet, highly efficient, and optimized for your resin? → Infinity Series
- Conveying extreme distances (1000+ equivalent feet) where a claw pump is truly required? → UVP Series
Final Thoughts: Smart Choices for a Smarter Plant
At the end of the day, the best vacuum pump isn’t just about moving material—it’s about doing it efficiently, quietly, and without unnecessary costs or headaches.
Whether you need a standard workhorse, a quiet upgrade, a long-distance powerhouse, or the latest advancement in PD technology, there’s a solution built for you.
Curious to learn more? Mosey on over to Novatec’s Vacuum Pumps page—or give us a holler using the form below.
No sales pitch. No pressure. Just a conversation about what’s right for your plant.
Because the right vacuum pump isn’t just another piece of equipment—it’s the key to smoother processing, greater efficiency, and a more productive operation.
Let’s figure it out together!
Submit A Question: Conveying
Ask the Expert
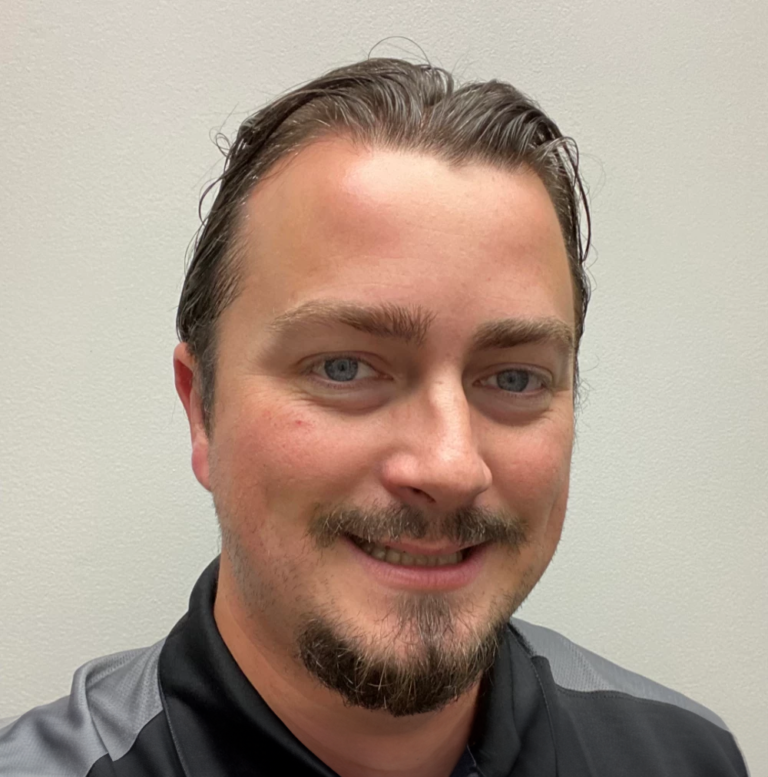