Press-Side vs. Central Plastic Resin Drying
How to select whether press-side or central plastic pellet drying works best for your processing location.
There are, of course, reasons why press-side resin dryers may be best for some processors but more and more are converting to central systems because their production requirements have changed over the years. Once they make that change, they will never go back because the economic advantages of a central system are very favorable to most processors profit margins.
Let’s examine:
- Reasons for maintaining a plastic resin press-side arrangement
- Reasons for considering a plastic resin central drying system
- Economic benefits of a plastic resin central drying system
PROCESS AND REGENERATION FILTERS
Press-side or press-mounted resin dryers are commonplace where processors have fewer than 10 process machines and have low throughputs on those machines (under 25 lb/hr). It also helps if the processor is running the same material on the same machine day-after-day, making very few material changes. This requires that there be a vacuum loader at each machine and a source of material (usually a bulk box or drum of resin). Disadvantages of this type of arrangement include the need for constant fork-truck traffic and room to deliver material to the presses, and access to the machine throat. Still, this arrangement seems to work for this group of processors.
The interim move to a central system for most processors is to introduce multiple portable dry/convey units. These dryers are usually mounted on a cart with a drying hopper, a loader or receiver to supply resin to the drying hopper and a machine-mount loader or receiver to deliver material to the machine throat. The throughputs range to approximately 200 lb/hr. The bulk boxes and forklifts are still present – clogging up the production area. If multiple material changes are required, processors often have extra dry/convey units in an area off the production floor that can be wheeled into place beside the process machine. This can add to the confusion on the production floor and the whole process often results in material being left in the bulk bins and/or contaminated and simply wasted.
Yet another scenario occurs when a processor needs throughputs higher than 200 lb/hr. In this case, larger stationary dryers are introduced but, they take up valuable floor space. Or, they are mounted on racks above process machines. In these cases, routine maintenance will probably not be performed as needed – ultimately resulting in excessive rejected parts and higher energy bills.
It should be noted that even when you are drying the same plastic pellets in different dryers (even of the same model) you may experience variation in the levels of drying. Reasons for this difference include, the age of the desiccant, heaters, blowers, or even the condition of the filters.
WHAT IS CENTRAL DRYING?
Central drying systems allows one dryer to provide -40°dew point air to multiple material hoppers of different sizes. An adjustable heater and blower are mounted on each hopper so the heat and air flow can be adjusted to the material in that hopper. This arrangement allows for custom drying of multiple materials from a single central dryer that is sized to match the requirements of the bank of hoppers. Central plastic pellet dryers are available with throughputs from <200 lb/hr through 5,000 lb/hr, which meet a wide a wide range of processor needs. Processors often have more than one central dryer – each serving a bank of hoppers with a back-up central dryer for times when a dryer may be taken offline for maintenance.
YOU ARE A GOOD CANDIDATE FOR CENTRAL DRYING/CONVEYING IF…
- You have dryers on 10 or more machines.
- You have a single material that requires drying at multiple machines.
- You have frequent material changes on your machines.
- You use more material types than you have machines.
- You have dryer-to-dryer quality issues when drying the same material.
- You want to expand, but do not have sufficient space.
- You need flexibility to serve the needs of your customers.
- You have a Just-in-Time objective to reduce inventory.
- You need to reduce operating costs.
- You want to improve safety for your workers.
WHAT ARE THE BENEFITS OF CENTRAL RESIN DRYING?
Here is a brief overview of the benefits:
- Space savings
- Fewer materials handlers
- Energy savings (rebates often available)
- Increased machine uptime (no waiting for material to pre-dry)
- Material control reduces waste (small inventory to clean)
- Improved product quality (drying consistency through your plant)
- Fast payback of investment (because there are multiple sources for savings)
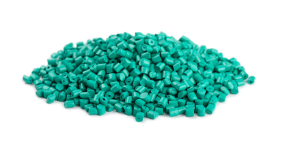
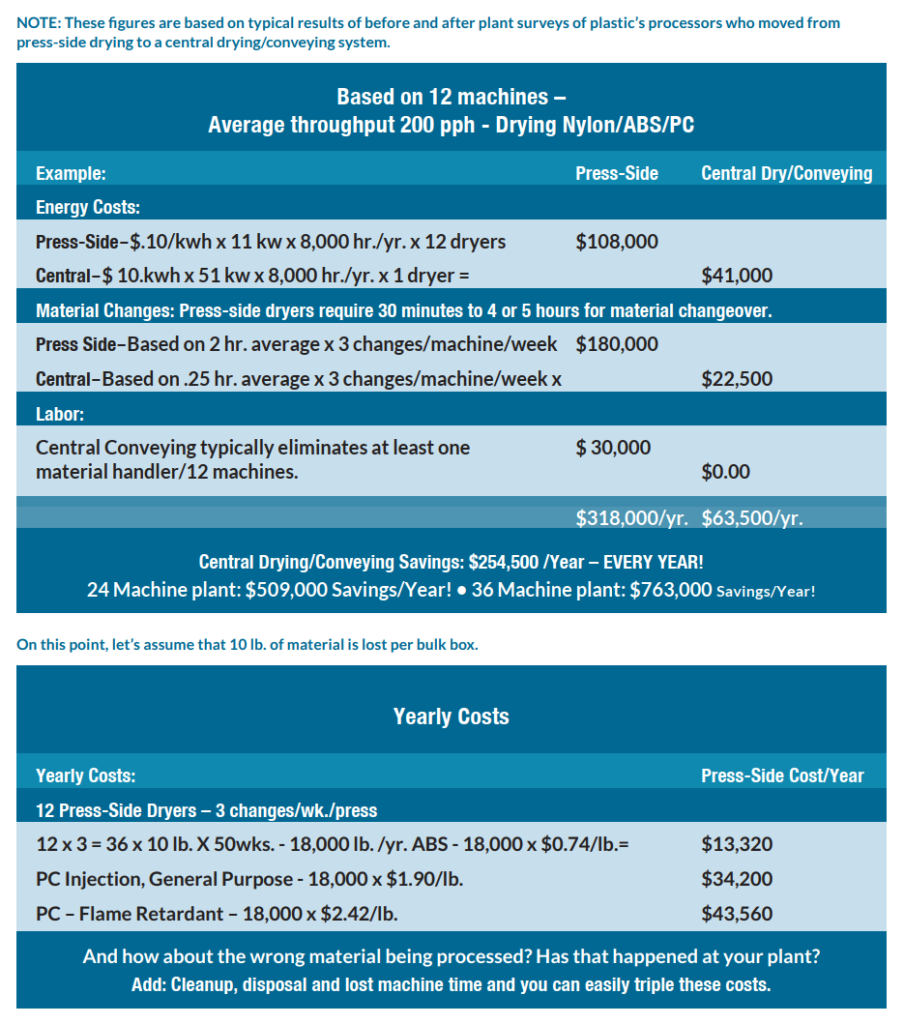
ADDITIONAL SAVINGS NOT CALCULATED:
- Maintenance on 12 dryers vs. 1 Central Dryer
- Brush changes and filter cleaning for 12 loaders vs. just filter cleaning for 12 vacuum receivers
- Energy usage for 12 dryers and 12 loaders vs. 1 dryer and 1 vacuum pump
- Loss of material due to bulk box movement, material contamination and poorly made parts
LET’S TALK ABOUT SPACE!
Typically, a processor using press-side dryers needs to allow and extra 75 sq.ft. per process machine for a dryer, hopper and bulk box. Now add the space required for a fork lift to maneuver in, haul the old bulk box away and replace it with a new one…
Suddenly, you are up to about 120 sq. ft.! Multiply that by the number of presses you have and you will see how many additional presses you can fit into that space – that, after all, is supposed to be your manufacturing area – where profits are made.
CENTRAL CONVEYING – ADDS BENEFITS TO CENTRAL DRYING!
Reduced Material Costs – Central conveying may allow you the option of buying materials in bulk for silo storage with a “free” silo from your material supplier or you may be able to increase your purchases to a point where it is advantageous to use bulk bins for storage instead of bulk boxes. But, even if you continue with bulk, they can at least be stored in a designated area where one person is responsible for ensuring that the material remaining in the liners is emptied into the new container and they are properly covered to prevent contamination.
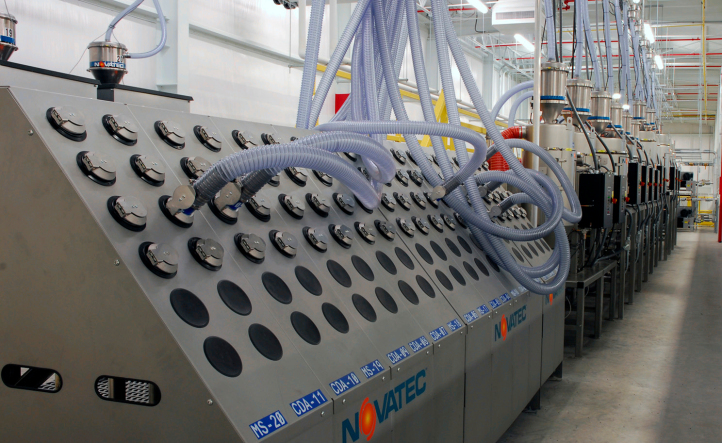
Quick and Correct Material Changes – Central conveying can reduce material changes to approximately 15 minutes. And, with Auto ID validation of materials, you can be sure that the right material will always go to the correct machine.
Safety – Reduced material spillage means safer conditions on the production floor.
A central drying/conveying system can pull materials from a combination of silos, bulk bins and bulk boxes to drying hoppers, or blenders or a combination
of those.
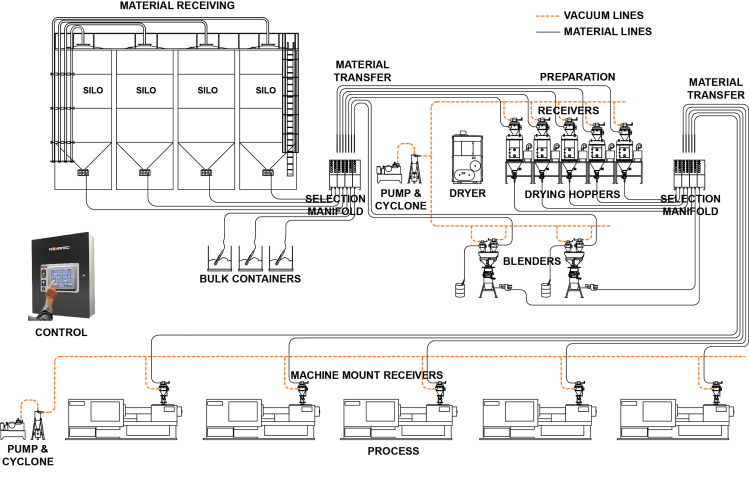
NEED HELP MAKING A DECISION ABOUT CONVERTING TO A CENTRAL RESIN DRYING AND CONVEYING SYSTEM?
Ask the Expert
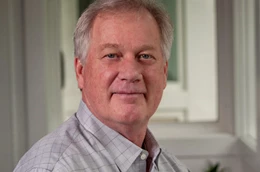