Trouble Shooting Guide for Wheel Dryers
The wheel dryer is a desiccant dryer. These are the most predominant dryers in service today. It uses a continuously turning wheel of desiccant that generally provides a very consistent dew point and temperature to the process. However, there are some things you need to know to address issues that you may see.
THE DRYER WILL NOT START
a. Power issues – Is there power getting to the dryer and the dryer controls? This could be because the dryer main circuit breaker or disconnect are not turned on. Check to see if the dryer has the proper power and voltage. If the dryer is getting power but the controls are not, check the control transformers secondary fuse.
b. Alarm Faults – Did the dryer shut sown in an alarm condition? Dryers have safety features that insure they don’t start until there is a corrective action for
major faults.
c. Phase issues – Is the dryer seeing power on all phases? Is there correct rotation on the blowers? Was there a blower fault such as pulling too many amps?
THE HEATER WILL NOT START
a. Safety Interlocks – Most process heaters, have an interlock to ensure that the heater does not come on if the process blower is not running.
b. Blower rotation – The heater may not start in the event of incorrect blower rotation.
c. Flow Switch – There may be a flow switch so that the heater doesn’t come on if the air flow is low enough that there could be an overheat condition. This could be caused by dirty filters or clogged lines with fines or volatiles.
THE DRYER IS NOT MAKING THE CORRECT DEW POINT
a. Return Air Temperature – Most dryers need no more than a 140 F return temperature to the desiccant so that it operates properly. If the return temperature is too high, it can be difficult to make a -40 dew point. It may be necessary to use cooling water at the return air cooling coil.
b. Dew Point Sensor – Generally the dew point sensor needs to be replaced yearly. Ensure it’s in proper working order
c. Desiccant condition – Is there any dust or volatile contamination of the desiccant? If so, replace it.
d. High return dew point to the desiccant– There are limits to how much moisture the desiccant can adsorb. If there is excessive moisture coming from the resin (i.e. surface moisture or from excessive hydration) the desiccant may not be able to achieve the required dew point performance.
e. Insufficient regeneration heat or flow– Check your regeneration filters and the regeneration inlet and discharge temperature. If the filters are dirty, replace them? If the inlet temperature is below that specified by the manufacturer, check to see if the heating element is operating properly. If the regeneration exhaust is less than 212 F, the air flow may be insufficient or the resin moisture may be beyond the dryers design limits.
MATERIAL IN THE HOPPER ISN’T DRYING PROPERLY
a. Dirty filters – If the air flow is reduced,the resin may not dry properly.
b. Hopper Residence Time – Is the hopper sized properly? Different resins require different drying times. Not all resins can be dried in 2-4 hours. This is especially true for resins with a low drying temperature or soft resins that can stick together if the drying temperature is
elevated.
c. Leaks in the System – The hopper and the conveying system need to be isolated from ambient and each other. Any leaks that can cause the dry air to leave the system should be eliminated. This is also true of hoses and ducting.
d. Incorrect drying temperatures – Try to follow the manufacturer’s recommendations. For instance, not all grades of the same resin class should be dried at the same temperature. (i.e. not all nylon 66’s
are the same) Also, are all of the elements in the process heater working? At
times, this can lead to lower than designed drying temperatures.
e. Hopper Level – Is the hopper level being controlled at too low a level for the residence time necessary?
f. Dew Point Performance – There must be a driving force for the resin’s moisture to leave it for the air stream. Is the dryer operating at it should per the previous section? Dew points higher than -40 can indicate that the dryer isn’t performing to specifications.
g. Wheel Speed – Is the wheel rotating at the manufacturer’s specified speed?
MATERIAL MELTS OR BECOMES VERY “TACKY” IN THE HOPPER/ DOES NOT DISCHARGE PROPERLY
a. Process Drying Temperature – Has the manufacturer’s recommended drying temperature been exceeded? Most dryers have minimum temperatures that the can operate. Part of this is because there is a temperature rise across the process blower (heat of compression)
and another rise across the desiccant (heat of adsorption). You may need cooling water prior to the desiccant and/or following it to achieve the manufacturer’s recommended temperature. This is a typical occurrence with copolyesters and bio-resins.
b. Wheel Speed – Generally high wheel speeds lead to higher discharge temperatures. This is because the time in the cooling section is reduced. Discuss changing the wheel speed with the dryer’s manufacturer.
c. Low Air Flow – Low air flow could lead to less cooling and higher discharge temperatures. Check your filters and consider adding a flow switch alarm if it wasn’t provided with the dryer.
d. Resin type – Some resin types, like elastomers, have issues with bridging. Tall hoppers can lead to high pressure on the resin at the bottom of the hoppers, and compression that leads to bridging. Soft resins may require special hopper designs, or agitation, that limit this issue. Many dryers today give you recommendations for solving issues. Please note the alarms given by the dryers and correct any issues. For further information, check the instruction manual or discuss the problem with the vendor’s service department expert.
Ask the Expert
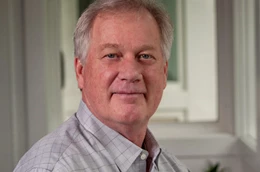