Desiccant Wheel/Rotor Dryers
This is not your father’s type of desiccant dryer! Desiccant wheel dryers are far more efficient, more compact, and require less maintenance than any previous dual bed desiccant dryer.
If you are familiar with old technology dual bed/twin tower or ‘carousel’ dryers, you think of desiccant as a large volume of B-B-sized round beads that are composed of about 30% clay.
Desiccant wheel dryers are entirely different in that the desiccant is pure molecular sieve desiccant that is literally grown onto a synthetic substrate, which is rolled into a round shape and encased in stainless steel.
What is a Desiccant Wheel Resin Dryer?
A desiccant wheel resin dryer is a type of dryer used to remove moisture from plastic resin. It uses a desiccant wheel, which is a rotating drum that contains a desiccant material, such as silica gel or molecular sieves, to dry the resin.
The operation of a desiccant wheel resin dryer involves passing the moist air through the desiccant wheel, which absorbs the moisture. The dry air is then passed over the resin, drying it to the desired level. The desiccant wheel rotates continuously to ensure that the desiccant material is evenly distributed and the drying process is efficient.
One of the advantages of a desiccant wheel resin dryer is that it can operate at a low temperature, which is important for preventing thermal degradation of the resin. Additionally, it is capable of removing moisture from the air even at high humidity levels, making it suitable for use in humid environments.
Advantages of Desiccant Wheel Dryers:
- Lower energy usage
- Less surface area of metal to heat
- Compact pure crystaline desiccant
- Up to 75% less footprint
- No spikes or deviations in temperature or dew point because there is no “Bed-Changing”
- Less maintenance
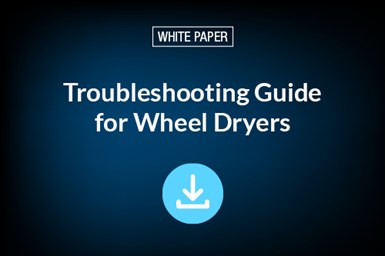
How a Desiccant Wheel Dryer Works
As the desiccant wheel rotates, stationary seals divide it into 3 distinct sections: Drying, Regeneration and Cooling. This continuous process ensures that dry desiccant is always available, therefore:
- Efficiency increases
- Power consumption decreases
- -40° dew point is guaranteed
Drying Section – A process blower pulls saturated air from the hopper and through a process filter and cooling coil. Process air is forced through the drying section of the desiccant wheel where the moisture is adsorbed. The desiccated air is then heated to the required temperature for drying and circulated back through the resin hopper.
Cooling Section – The desiccant is prepared to adsorb moisture when it rotates to the drying section.
Regeneration Section – Ambient, filtered air is heated to 400° F and forced through the regeneration section removing the moisture that was adsorbed by the desiccant.
Controls – Manufacturers have different controls for their wheel dryers. Some use microprocessor controls. Some use color touch screens that are not PLC’s. These controls often use complicated “look-up” codes to identify errors or to convey other information. Others use advanced high resolution color touch screen PLC controls with clear written messages to explain errors or as reminders of maintenance operations that are due.
Types of Resin Drying Systems
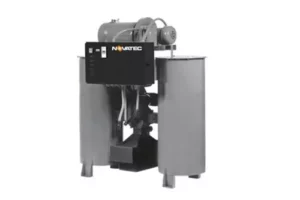
Silo Dehumidification/ Hot Air Dryers
What is a silo dehumidifier and how does it work and compare with other resin drying systems?
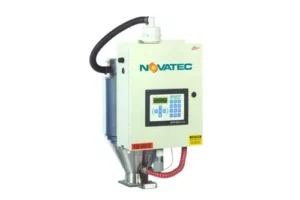
The principle of compressing air in factories for power tools and other high-pressure uses has a side benefit for the world of resin drying.
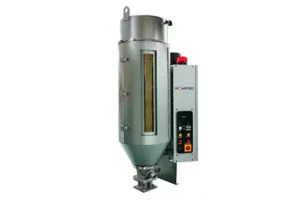
What is a membrane resin dryer and how does it compare to a compressed air dryer without a membrane?
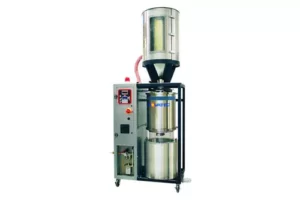
What is a vacuum resin dryer and how does it draw moisture away from plastic pellets in vacuum processing?
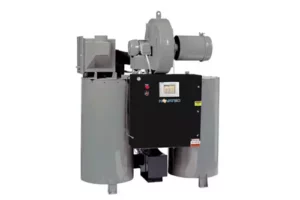
Dual Bed (also called Twin Tower) dryers used to be the most commonly purchased type of resin dryer. A look at why, and where the technology has progressed.
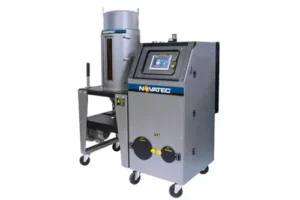
The advantages of desiccant wheel dryers include operating at a low temperature, which is important for preventing thermal degradation of the resin.
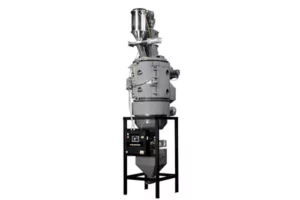
Technically, crystallizers are not dryers. They are used to convert PET from an amorphous, back to a crystalline state for re-processing.
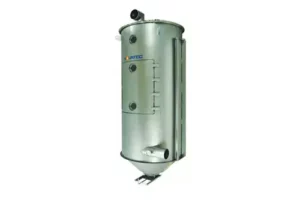
Drying Hoppers for Plastic Resins
Drying hoppers are part of most drying systems. At a glance, they look much the same, but there are certain features you should look for.
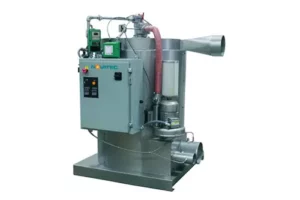
What are the benefits of gas-fired process heaters for drying plastic resins?
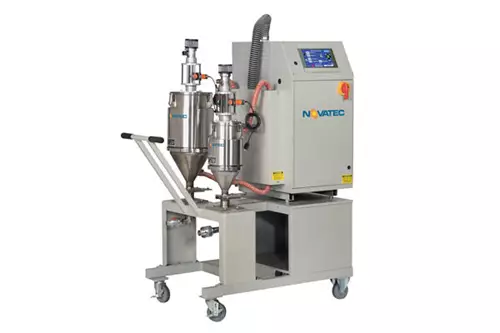
Resin drying machines that can be moved from machine to machine within a plastics processing plant have advantages and disadvantages over a central drying system.
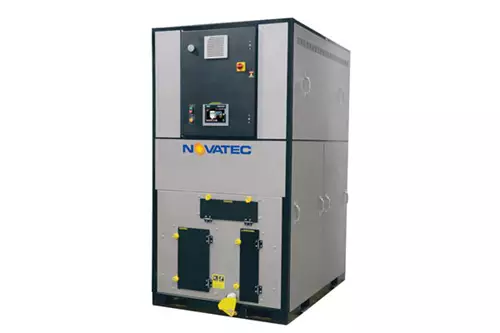
Properly designed Central Drying Assemblies are easily connected together to save installation costs.
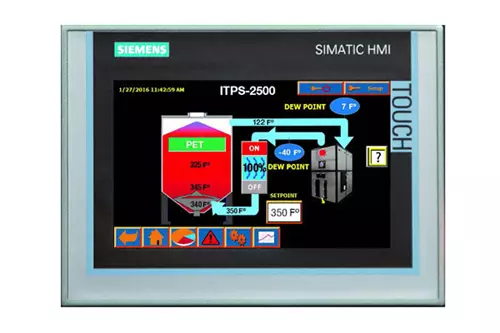
PET Energy-Saving Drying Systems
Learn about the keys to drying PET efficiently while saving space and energy.
Ask the Expert
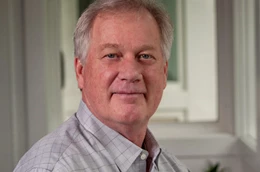